So werden Stillstandszeiten zu Betriebszeiten
2022-05-30
4 min read
„Was nicht kaputt ist, soll man nicht reparieren“, klingt auf den ersten Blick völlig logisch und vernünftig, doch tatsächlich es ist keine gute Faustregel. Außerplanmäßige Stillstandszeiten und schlechte Anlagenqualität kosten die Fertigungs- und Prozessindustrie Schätzungen zufolge jedes Jahr 20 bis 60 Milliarden Dollar. Dies hängt mit der bestehenden Zurückhaltung bei der Implementierung und Nutzung neuer Technologien zusammen, die zum Teil wohl auf die damit verbundenen Investitionskosten zurückzuführen ist, und unglücklicherweise Fortschritte bei Betriebsabläufen verhindert.
Auch wenn Anlagenausfälle wahrscheinlich niemals ganz vermieden werden können, so sollten sie doch keine bedeutenden Stillstandszeiten verursachen, den Unternehmensgewinn auffressen oder Hersteller dazu zwingen, sich finanziell zu verausgaben. Heutige Fertigungsanlagen sind weitaus komplexer als jemals zuvor, da sie Datennetzwerke, integrierte Hardware sowie eine Vielzahl automatisierter Systeme umfassen. Dies führt dazu, dass die von den meisten Herstellern angewendeten Instandhaltungsmethoden unzureichend sind. Tatsächlich zeigt ein Bericht von Infraspeak, dass 93 Prozent aller befragten Unternehmen ihre eigenen Instandhaltungsprozesse für wenig effizient halten.
Prädiktive Instandhaltung bietet die Möglichkeit, alle denkbaren Hardware-Ausfallszenarien vorherzusagen, festzustellen, wann Instandhaltungsarbeiten erforderlich sind, bei Bedarf Instandhaltungspersonal zu alarmieren und präventive Lösungen vorzuschlagen.
Alle, die in der Fertigung tätig sind, sind sich bewusst, dass Ausfälle und Defekte zum Alltag in der Branche gehören. Das Ziel der prädiktiven Instandhaltung besteht nicht nur darin, solche Ausfälle zu verhindern oder zu reduzieren, sondern auch darin, dazu beizutragen, dass Fertigungsanlagen hohe Effizienzstandards erreichen und im Verlauf dieses Prozesses hochwertige Produkte liefern. Ein Programm zur prädiktiven Instandhaltung kann unerwartete Ausfälle um bis zu 90 Prozent reduzieren, wodurch Ausfälle nahezu eliminiert werden.
Um prädiktive Instandhaltung in der Fertigung effizient umzusetzen, sollten Werksleiter so viele Daten wie möglich erfassen. Dies ist vor allem bei der Implementierung einer präventiven Instandhaltungsstrategie von entscheidender Bedeutung, denn je mehr Daten für die Analyse zur Verfügung stehen, desto präziser können Panne vorhergesagt werden.
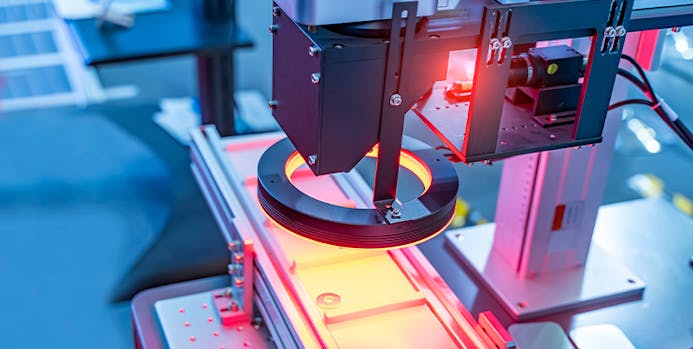
Gefahren aufspüren
Ein guter Start für eine solche Strategie wäre beispielsweise der Einsatz intelligenter Sensoren. Diese, zusammen mit Algorithmen für maschinelles Lernen, helfen bei der Erkennung von Anomalien in Industriemaschinen. Beispielsweise können intelligente Sensoren, die Daten in industriellen IoT-Umgebungen sammeln, die Temperatur von Ausrüstungskomponenten im Auge behalten und abgenutzte Teile, etwa fehlerhafte Schaltkreise, identifizieren.
Ebenso können spezialisierte intelligente Sensoren Vibrationsanalysen an bestimmten Komponenten durchführen und dabei eventuell vorhandene Ausrichtungsprobleme, verbogene Achsen oder andere Motorprobleme identifizieren. Anhand dieser Daten können Hersteller eine Analyse ihrer kritischen Anlagen durchführen, um Fehlermodi festzulegen. Dabei liegt der Schwerpunkt auf der Häufigkeit von Ausfällen, dem Schweregrad von Maschinenausfällen und der Schwierigkeit, Ausfälle zu erkennen.
Werden Zustandsüberwachungsgeräte mit einem computergestützten Instandhaltungsmanagement-System (computerized maintenance management system, CMMS) verbunden, können Werksleiter Warnmeldungen einrichten, damit das Instandhaltungspersonal über etwaige Defekte oder Anomalien an der Ausrüstung informiert wird. Auf diese Weise können Instandhaltungsarbeiten geplant und termingerecht durchgeführt werden, wenn bekannt ist, dass Bauteile ersetzt werden müssen, was die Wahrscheinlichkeit für das Auftreten schwerwiegender Ausfälle praktisch auf Null reduziert.
Beispielsweise kann entsprechende Sensortechnologie in mehrere verschiedene Fluidtechnik-Produkte niedriger Klassenebene integriert werden – von Steckverbindungen, Schläuchen und Rohren bis hin zu Pumpen, Motoren, Stellgeräten und Filtern. Diagnostische Daten, die von Steuerungsventilen erhoben werden, können in solchen Szenarien bei der Behebung von Problemen mit fluidtechnischen Anlagen von zentraler Bedeutung sein.
Neuere Maschinen bieten in der Regel unterschiedliche Optionen für die Datenerfassung in Echtzeit, doch auch Altausrüstung kann durch die Nachrüstung mit kostengünstigen Sensoren ergänzt werden. Prädiktive Instandhaltung kann eine wichtige Ressource im Umgang mit alternden Anlagen sein, für die eine sorgfältige Planung zur Beschaffung obsoleter Ersatzteile notwendig ist.
Auch wenn ein gewisses Ausmaß an Anlagenausfällen unvermeidbar ist, sollte diese Tatsache nicht zu ungeplanten Stillstandszeiten und schlechter Anlagequalität führen, was die Fertigungs- und Prozessindustrie jedes Jahr Milliarden kostet. Vielmehr hilft ein ausgereifter und effektiver Plan zur prädiktiven Instandhaltung, das Auftreten von Stillstandszeiten weitestgehend zu vermeiden, erheblich zu reduzieren und gleichzeitig die Rentabilität Ihrer Anlage durch gesteigerte Betriebszeiten stark zu erhöhen.