Powder Bed Fusion: Transforming production processes
2025-02-18
9 min read
In the ever-evolving world of Additive Manufacturing (AM), Powder Bed Fusion is emerging as a key technology. Industries are increasingly looking to it to enhance their design and production capabilities.
Are you looking to adopt Powder Bed Fusion on your factory floor? If so, let’s explore why this manufacturing method is gaining traction. As well as, the benefits and challenges it brings to the table.
What is Powder Bed Fusion (PBF)?
Among various Additive Manufacturing technologies, Powder Bed Fusion (PBF) [1] stands out as favourable. It is a versatile production process that can use many different materials.
A high-powered heat source—typically a laser or an electron beam—selectively fused regions of a powder bed. Parts are constructed layer by layer with remarkable accuracy. This process allows for the creation of complex designs that cannot be achieved with conventional manufacturing methods.
This speciality has applications across multiple fields. It ranges from the production of microcomponents and complex biocompatible structures to the manufacturing of aerospace and automotive parts.
How does PBF work?
The process creates parts in a layer-by-layer manner. It involves spreading a thin layer of powdered material over a build platform [2].
Next, a focused energy source scans the layer. It fuses the powder in the area where the part will form. Many powder materials can be used in this process, including polymers, ceramics, and metal alloys. Once the layer completes, the build platform lowers, and the system applies a new layer of powder.
This cycle continues until the process completely forms the part. The process utilises resources more efficiently compared to traditional methods, in part due to the capability to reuse powder. That’s why aerospace, medical, and defence industries are adopting PBF as a primary production process [3].
Variants of PBF
Powder Bed Fusion isn’t a one-size-fits-all approach. Different variants cater to diverse materials and end-use requirements:
Selective Laser Sintering (SLS):
Selective Laser Sintering is a specific type of Powder Bed Fusion technology. A laser beam is used to fuse powdered materials together in this technique. This paves the way for the creation of complex geometries with many purposes. [4]
SLS has been mainly used for creating prototypes and end-use parts. This process uses thermoplastic polymeric materials like nylon, polyester, polyvinylchloride, and acrylonitrile butadiene styrene, among others. The use of low-power laser energy sources leads to its effectiveness.
Selective laser sintering 3D printing [5] is known for its affordability and speed. It is able to create complex shapes and offers a growing range of materials to choose from. Because of these features, it is perfect for making prototypes fast. It is also useful for assembling functional prototypes, creating parts before full production, and making test rigs.
Another advantage of Selective Laser Sintering is its ability to print parts with thin walls and intricate internal structures. This makes it a favourite in fields like aerospace, automotive, and medical devices.
Direct Metal Laser Sintering (DMLS):
A laser that is somewhat low-powered is used for DMLS. This is where two or more metal powders with different melting points are mixed. The high melting point powder serves as the structural material, while the low melting point powder acts as the binder.
Direct metal laser sintering offers many benefits, including the ability to produce accurate and precise parts and a shorter production cycle. The absence of binder materials also greatly reduces post-processing procedures.
Electron Beam Melting (EBM):
EBM uses a powerful electron beam to melt metal powder, leading to high production speeds and throughput. The high temperatures involved lead to parts that have minimal internal stress. Furthermore, a clean and controlled build is assured by the vacuum environment.
Electron Beam Melting utilises an electron beam instead of a laser. Because of this, it can be useful when dealing with metals that melt at high temperatures, like titanium alloys. Building with a vacuum also helps to maintain material purity.
This technology is often used to make custom implants or prostheses in the medical field. Both strength and biocompatibility are essential in these cases.
Is PBF suitable for your business?
For many different types of manufacturing, PBF is the method of choice due to its many benefits:
Resource optimisation
The PBF process is highly efficient regarding materials. It minimises waste and optimises material usage, which makes it an environmentally sustainable choice. Also, powder is used precisely so that there is very little waste, which helps conserve resources and lowers production costs.
Design flexibility
Complex geometries and internal structures can be created with PBF, which is not possible with usual manufacturing processes. The aerospace, medical, and automotive industries greatly benefit from this capacity to generate complex designs.
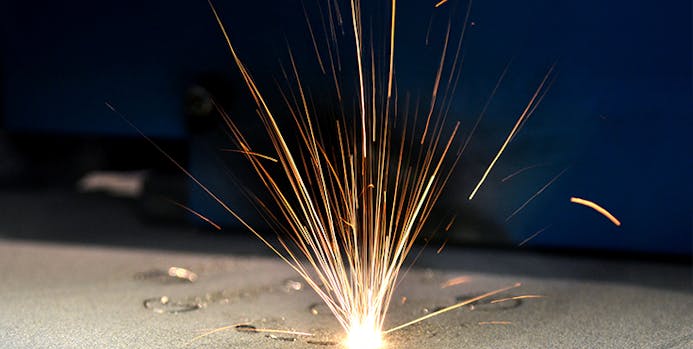
Efficient resource usage
PBF is more efficient than traditional manufacturing methods. It reduces the amount of material waste by only using the powder that is required for the build.
The precise use of powder leads to both resource conservation and reduced production costs.
Recyclability of powder
You can gather any unused powder and reuse it in later builds. This ensures efficient resource use and helps reduce environmental impact. This is particularly crucial for industries with a focus on sustainability. This recycling of powder is a vital aspect of making powder-based manufacturing (PBF) a green production approach.
Enhanced mechanical properties
PBF, particularly when using metal powders, produces parts with excellent strength and durability. Industries that rely heavily on the safety and reliability of their parts, such as aerospace and automotive, will greatly benefit from this. Parts produced through PBF exhibit superior mechanical properties, making them suitable for critical applications.
Applications of PBF in industries
Aerospace
The aerospace industry has gained major benefits from PBF. This technology is especially useful in producing lightweight components that boost fuel efficiency and enhance overall performance.
Lightweight structures
PBF is employed by aerospace engineers to produce lightweight structural parts [6]. Engineers can use high-strength materials such as titanium and aluminium.
This approach helps to reduce the weight of an aircraft. As a result, it leads to lower fuel consumption and longer flight ranges. The capability to produce complex geometries without support structures expands design possibilities.
Powder Bed Fusion allows a high level of precision. This makes it possible to manufacture complex engine parts that would be difficult to make using more conventional processes. This helps ensure that critical applications are safe and reliable and that aeronautical components are up to par with industry standards.
Automotive
PBF is also used in the automotive industry. It serves both prototyping and the production of end-use components. This method provides flexibility and efficiency in manufacturing. [7]
Prototyping
Automotive designers utilise PBF for rapid prototyping. This approach allows for quicker design cycles and testing. As a result, it fosters innovation and speeds up development times.
End-use parts
PBF is used to create durable and high-quality parts for vehicles. This process ensures that automotive parts can meet the rigorous demands of the industry. From engine components to interior parts, PBF provides a versatile and reliable solution for manufacturing.
Medical
Powder Bed Fusion is vital in the medical field. It is used to make custom implants and prosthetics that meet the specific needs of each patient.
Bespoke implants
PBF is used to produce implants tailored to a patient's unique anatomical requirements [8]. These implants, which are often made from biocompatible materials, provide a perfect fit and function while cutting prices and lead times to a minimum.
Prosthetics
The medical sector gains advantages from PBF's capability to produce prosthetic limbs. These technicians design these limbs with high precision and optimal mechanical properties, enhancing comfort and functionality for users. Furthermore, the cost efficiency of metal PBF makes the production of prosthetics more accessible.
Disadvantages of Powder Bed Fusion
Despite all of the benefits, there are still a few obstacles with PBF:
Financial considerations
Equipment and materials
PBF requires a significant initial investment in both equipment and materials. Laser-based systems can be quite costly. Also, the use of premium materials like titanium and aluminium powders adds to the overall high expense. Because of this, PBF may be beyond the reach of startups and smaller firms who have limited budgets.
Maintenance and operational costs
To keep PBF machines performing at their best, operators must conduct regular maintenance. The complex nature of these machines often requires specialised technicians for maintenance, which drives up operational costs. Because of these ongoing costs, PBF may end up costing more than other production processes.
Technical challenges
Size limitations
For the most part, PBF works better when making smaller, more intricate components. Size restrictions in the build chamber limit the maximum size of the components that it can produce.
Process optimisation
The quality of the final product relies heavily on several factors. These include laser power, scan speed, layer thickness, and powder quality. Changing any of these elements can have an adverse impact on the quality of the finished product.
Post-processing requirements
Parts produced through PBF often need extensive post-processing. This includes the removal of unused powder, heat treatment, and surface finishing. These extra steps can increase production time and costs, reducing the overall efficiency of the process.
Conclusion
PBF technology marks a notable improvement in manufacturing capabilities. It provides unique benefits related to design freedom, material efficiency, and part quality. While challenges exist, continuous technological improvements and standardisation efforts are making PBF increasingly accessible and reliable for various industrial applications.
The successful implementation of PBF requires careful consideration of various factors. As the technology continues to evolve, staying informed about the latest developments and best practices will be crucial for maximising its benefits. Manufacturers can ease their transition to PBF technology by working with automation experts like EU Automation. This partnership helps them maximise the technology's potential for their unique applications.
Citations:
[1] Hussain, A., Abbas, N., Kwon, Y.S. et al. Transforming biofabrication with powder bed fusion additive manufacturing technology: from personalized to multimaterial solutions. Prog Addit Manuf (2024).
[2] https://www.sciencedirect.com/topics/engineering/layerwise Serge Abrate, Marco Di Sciuva, in Comprehensive Composite Materials II, 2018
[3] https://www.sciencedirect.com/topics/engineering/primary-production
[4] https://www.mdpi.com/1996-1944/18/2/447
[5] https://engineeringproductdesign.com/knowledge-base/powder-bed-fusion/#Selective_Laser_Sintering_SLS
[6] https://www.diva-portal.org/smash/get/diva2:1316708/FULLTEXT01.pdf
[8] A. Awad, F. Fina, A. Goyanes, S. Gaisford, A.W. Basit, Advances in powder bed fusion 3D printing in drug delivery and healthcare, Advanced Drug Delivery Reviews (2021) https://discovery.ucl.ac.uk/id/eprint/10127468/1/1-s2.0-S0169409X21001538-main.pdf