Industrial robots: Limitations and solutions
2023-06-20
4 min read
Almost all industries utilise industrial robots today, ranging from automotive to plastics and medical technology. They bring many benefits to manufacturing facilities and are paving the way for the smart factories of the future. Nevertheless, there are certain limitations manufacturers should consider when choosing their robotic equipment.
Fortune Business Insights predicts that the market for industrial robots will reach USD 31.3 billion by 2028. The demand for automated procedures is what is driving this. As manufacturers recognise the potential benefits of implementing robots in their operations, it is essential to acknowledge the limitations associated with these machines.
In this blog, we will explore three key limitations of industrial robots. This includes industrial robot costs, industrial robot safety, and the challenge of conducting industrial robot training. This will allow us to shed light on these obstacles and how manufacturers can overcome them.
1) Industrial Robot Costs
Industrial robots often require a significant upfront investment, including installation and configuration costs. Additionally, manufacturers must factor in ongoing maintenance expenses. These can vary depending on the robot's complexity and usage. However, it can add to a significant portion of the total cost of ownership.
Furthermore, the need for additional components, such as end-of-arm tooling or specialised sensors, can increase costs.
Similarly, robotics is a constantly evolving industry, with upgraded machines always appearing on the market. For some companies, investing in new robots regularly can be a struggle. This is especially true for smaller ones that risk going bankrupt in their attempt to keep up with industrial trends.
Can robotics be affordable?
However, industrial robots can help manufacturers cut costs in different areas. They can reduce production costs and increase profits by optimising work. With a clear investment strategy and financial plan, robots are most likely to bring a fast return on investment.
Another cost-effective option is to invest in reconditioned robots. These offer a similar efficiency and operability at a fraction of the cost of new ones.
2) Industrial robot safety
People have always viewed industrial robots as potentially dangerous when they are on the factory floor. And for good reason – they are huge, hulky pieces of equipment that can move at rapid speeds.
Older machines even lack the sensory capabilities to detect nearby humans, making them prone to dangerous collisions and accidents. For this reason, many manufacturers add cages or dividers to separate robots from their human co-workers. Therefore, increasing industrial robot safety.
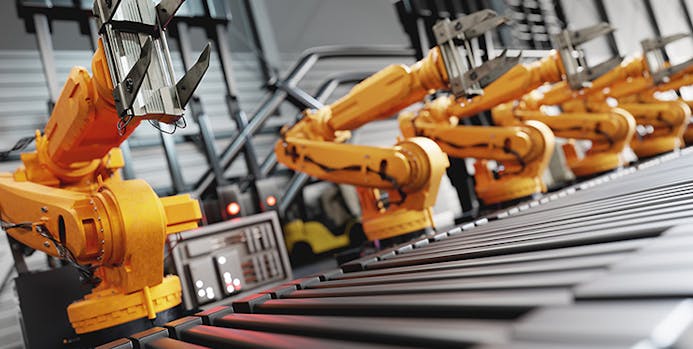
However, advancements in technology have led to the emergence of collaborative robots (cobots). Their sole purpose is to ensure that people can use them in a safe environment. Enhancing the safety of both traditional industrial robots and cobots has also involved implementing regulatory practices.
While absolute safety is still a work in progress, there are many effective methods for improving human safety. This includes ongoing advancements such as, light curtains, laser scanners, and presence-sensing devices.
In addition, conducting individual risk assessments of production lines can help improve workplace safety. Providing comprehensive training to workers on how to react to potential accidents is also beneficial.
By implementing these multiple strategies, companies can gradually enhance worker safety and foster a more secure and productive environment within robot-driven workplaces.
3) Industrial robot training
Industrial robots require expert programming and training, necessitating the hiring of experienced engineers and programmers during installation. Even experienced personnel may need retraining as new software or robot models enter the market. Incorrect programming can lead to malfunctions and pose risks to those working nearby.
Recently, the field of robot training has seen the implementation of a new method - no-code or low-code programming. It allows employees with less coding experience to configure a robot using visual modelling and drag-and-drop user interfaces.
Adjusting the arm of robots allows for easy reprogramming of different jobs. This is thanks to the user-friendly format of no-code and low-code platforms. Most companies would once require multiple robots. Now, a non-technical person can make a simple adjustment, saving companies time, space and money.
The trend of low- and no-coding platforms is rising. This is because 84% of businesses in the US, UK, Canada, and Australia have adopted low-code development environments. As a result, the amount of coding that is required will decrease.
There is no question that industrial robots have a lot of benefits. They make production more efficient and give manufacturers a quick return on their investment. However, it is crucial to address their limitations proactively. Manufacturers can overcome challenges associated with industrial robots and fully leverage their potential in building smart factories of the future.
By putting effective planning into practice and looking into cost-cutting options, this is achievable. As well as, prioritising safety measures and adopting new training technologies.
Continue reading about the latest developments in industrial robotics by visiting EU Automation.