- 홈 >
- 산업 부문 >
- Paper, print & pulp >
-
Industry Report
Paper, print & pulp
The paper, print and pulp industry is one of the largest in the world. Manufacturers produce over 400 million tonnes of paper and cardboard worldwide every year. However, as we digitalise more processes in our everyday lives and in industry, will we see a fall in demand for paper-based products? EU Automation delves deeper and highlights the main trends, techonlogy and industry news, automation professionals worldwide need to take note of in our indepth industry report.
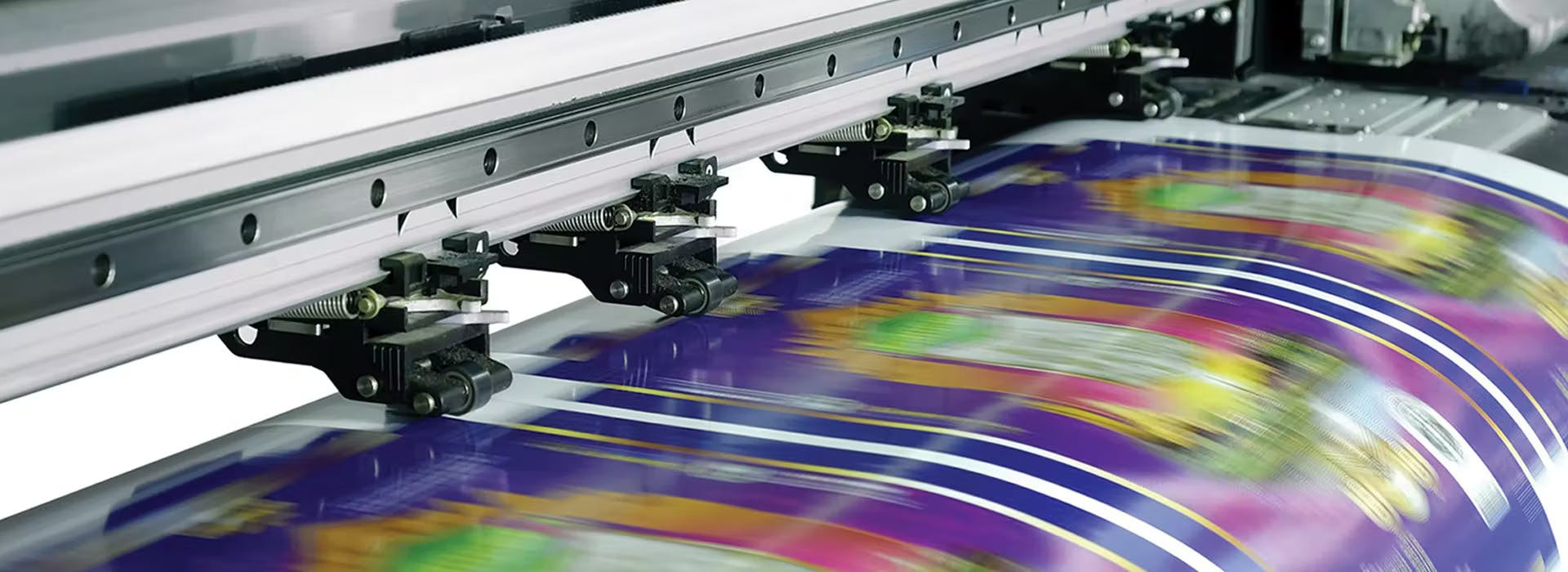
1. The paper, print and pulp industry now and in the future
The paper, print and pulp industry is one of the largest in the world. Manufacturers produce over 400 million tonnes of paper and cardboard worldwide every year. However, as we digitalise more processes in our everyday lives and in industry, will we see a fall in demand for paper-based products?
Paper has been one of the most widely used writing materials around the world since the Egyptians used papyrus. Now, we use paper every day — when we read the newspaper, open a parcel or hand a bank note over to a cashier.
As paper became more widely used, it influenced the development of the printing industry. Before printing, books had to be written by hand, limiting the amount of copies that could be produced. This also meant that few people were literate – only monks had access to books and an education. In the 15th century, the invention of the Gutenberg press changed this.
Early printers used moveable metal blocks of letters and symbols to create text and print it on paper, speeding up the process and contributing to increased literacy rates. We use similar methods to the Gutenberg press today. In offset lithography, for example, we use blocks to mass produce newspapers, books and other printed products to meet consumer demand. Now, nearly 130 million books have been published around the world.
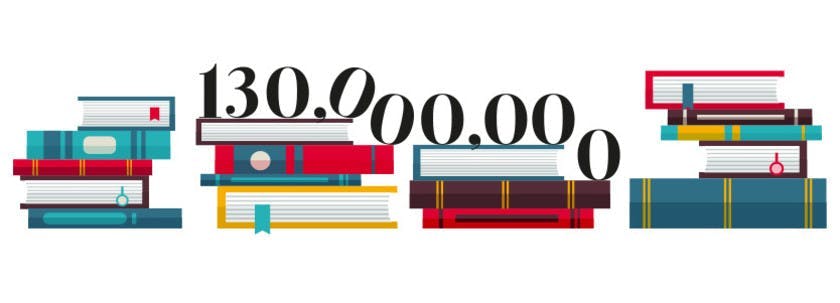
On paper
Manufacturers produce paper from connected fibres, sourced from wood, which can be either harvested or recycled. During the process, wood is ground to pulp, bleached or coloured and then fed into rollers to create paper. Once the paper has been left to dry, cut to size and given a finish, it is sent to be used for its intended purpose, for example for printing or packaging.
BCC Research reported that the global market for paper manufacturing reached $482 billion in 2017 and the industry employs around 647,000 workers in Europe. However, McKinsey reported that the worldwide demand for graphic paper has declined over the past few years and may continue to do so. Despite this, the paper industry is growing at a slow pace. Manufacturers should be aware of changes in the market to make sure they are not left behind.
Digitalisation
It is a common misconception that the adoption of computers will cause a dramatic decrease in demand for paper-based products. While people may prefer to record things digitally instead of on paper, the industry has not disappeared entirely — it has evolved to follow market trends.
For example, more people are choosing to purchase online with 79 per cent of American consumers using websites to shop. Paper manufacturers can benefit from the growth of online shopping, by supplying paper and card packaging to safely deliver products for customers.
Environmental considerations
Manufacturing paper both uses and produces a large amount of energy. Producing pulp and paper requires high levels of heat and electricity to reduce wood to pulp and form that into paper. The production process also produces energy that can easily be wasted.
For paper to be a more sustainable resource, manufacturers should consider how they can reduce energy consumption. For example, they could use the energy generated as a bi-product to power the mill, to reduce reliance on fossil fuels and cut energy costs.
Governments are currently looking to reduce our reliance on single-use plastics, particularly focussing on packaging. In the UK, a 5p charge has been introduced on plastic bags, that does not apply to paper. Supermarkets and other retail outlets may introduce more paper packaging to stay in line with this trend – a move which has already been made by Morrisons, which has introduced paper bags for loose fruit and vegetables. Paper is one of the most recycled materials in the world, so we may see an increase in demand of paper and card packaging to match the growing environmental concern over plastic use. However, manufacturers will have to ensure that paper bags are durable enough to be reused, to overcome the energy needed during the manufacturing process.
Manufacturers should consider how they can reduce the negative impact their mill has on the environment to improve sustainability and reduce energy costs, as this will help them stay competitive in the changing paper and pulp industry.
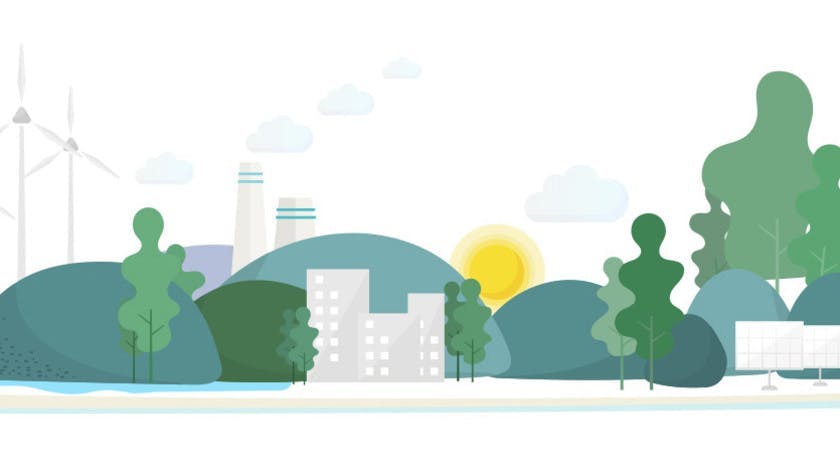
Resources
Paper manufacturers source raw materials at a very as cheaply as possible to keep production costs low. Chopping down the high volume of wood required as a raw material can have a detrimental effect on the environment and manufacturers will keep moving to new forests to cut costs.
To improve this process, manufacturers could find a more sustainable way to produce paper. For example, lower quality paper or card can be manufactured using recycled paper or resources such as sawdust, which decreases the amount of fresh wood needed. Manufacturers should consider the importance of sustainability to ensure their business maintains their production demand.
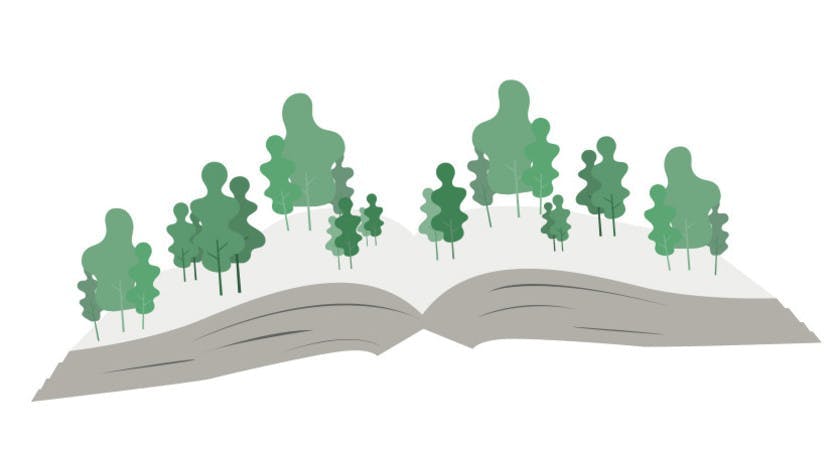
Automating the mill
As more companies require paper-based products for packaging, manufacturers should invest in equipment to improve productivity for their paper mill.
Automating a paper mill can increase flexibility and real-time control of processes in the facility. Manufacturers can install sensors and control systems to show the condition of machinery across the mill at any time, reducing the risk of unplanned breakdowns and downtime. Keeping the plant running efficiently with automation and connected sensors can help reduce energy costs and prevent any unplanned losses.
Manufacturers can also invest in automation to improve operations in a warehouse. Robotic arms can handle large paper rolls that are too heavy for humans to carry and can stack them higher than humans can reach. This can free up human operators for more complex or creative roles.
Automating manufacturing can improve safety, productivity and energy efficiency in a paper mill. As more people go paperless, manufacturers should embrace changes and invest in making products that consumers need. The demand for paper-based packaging is growing to match the pressure on reducing single-use plastic. Manufacturers must tap into consumer trends, technological advancements and developments in sustainable technology to ensure their business is as successful as possible.
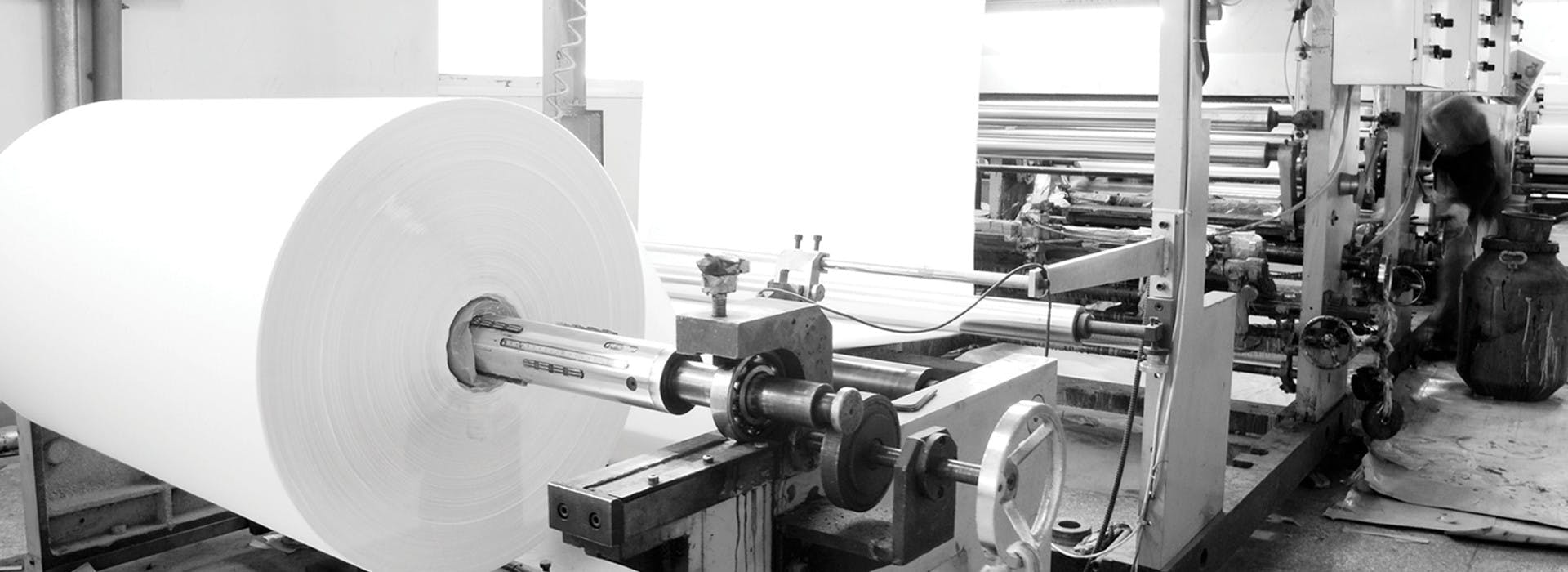
2. Adapting to survive
Changing demands of the paper industry.
According to research conducted by ACUVUE, the average office worker will spend 1,700 hours a year in front of a computer screen. This equates to six and a half hours a day spent on a computer or laptop. While we are printing less and typing more, that doesn’t mean the paper industry is suffering. However, paper and paperboard manufacturers must keep up with changing demands in a digital era.
Graphic paper, which encompasses newspapers and magazines to envelopes and A4 printer paper, has seen a steady decline for several years mainly due to the increased use of digital technologies. However, recent years have seen an increased demand for other paper-based products, keeping the industry thriving.
Industry challenge
The Strategic European Corrugated Report – 2018-2028 discovered a significant rise in the demand for corrugated cardboard over the past few years, with a 3.2 per cent increase year on year in Europe alone. This increased demand can be explained in part by the growing popularity of internet shopping. As consumers increasingly avoid the high street and order more packages and parcels online, manufacturers must prepare for a future of continued demand for corrugated carboard and adapt their facility to manufacture it efficiently.
Increased demand calls for a larger scale of production, meaning the rolls of paper must be loaded into an automatic splicer, a mechanical device for joining two pieces of paper. This is equipped with sensors and automatically feeds the paper through the corrugator one piece after the other. This automated process allows for continuous production to fulfil the high demands. If the splicer were to break down, continuous production would stop and cause major disturbance to the manufacturing line, this is where we can help.
EU Automation solution
Introducing automation increases output and improves productivity, but manufacturers do still worry about the cost of a breakdown. Luckily, this problem can be bypassed by integrating predictive maintenance. Predicting when machinery failures will occur means replacement parts can be ordered and delivered before that happens, making sure you’re always prepared.
If predictive maintenance isn’t feasible in your facility you can still rely on EU Automation to get your production line back up and running as quickly as possible.
As a specialised automation and obsolete parts supplier, we can locate source a replacement part and ship it to you quickly. Additionally, our guaranteed worldwide delivery of 48 hours or less makes sure you can continue production with as minimal downtime as possible.
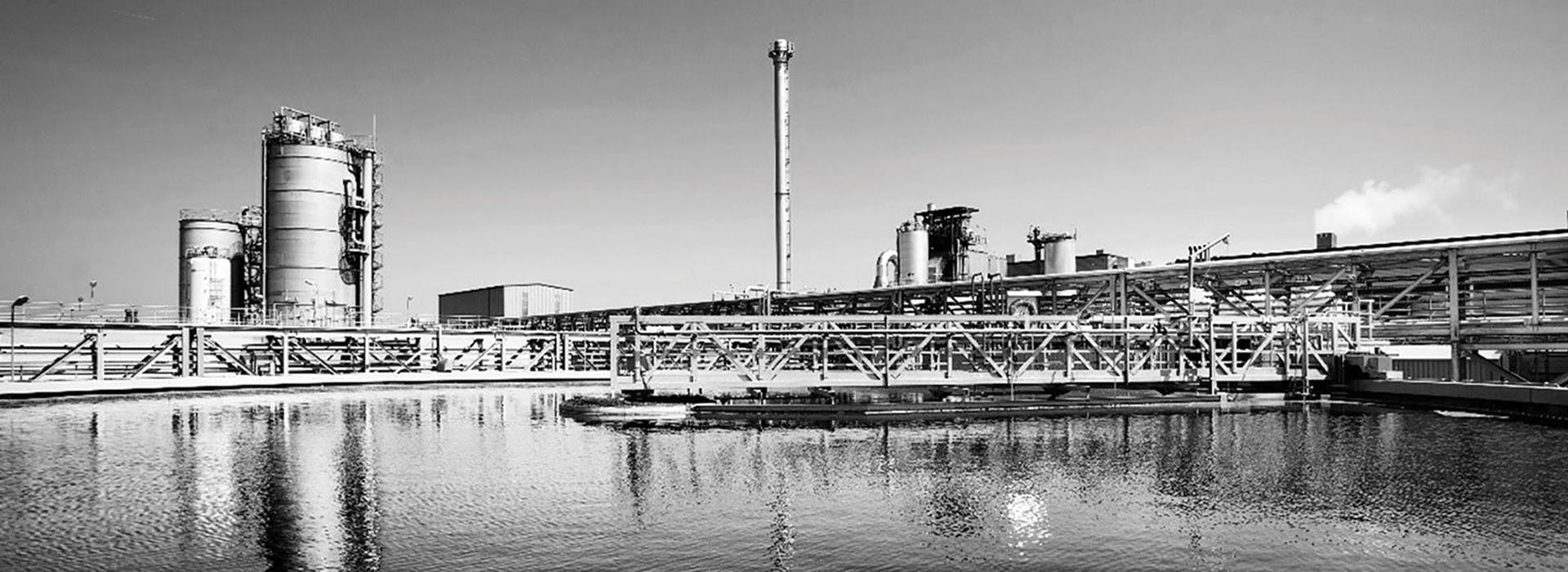
3. Paper and pulp – How we can help
The popularity of smart phones and computers means that you are far less likely to send a letter now than 20 years ago. Despite the mass adoption of technology, the world consumer over 413 million metric tons of paper in 2016. This is great news for manufacturers, but also contributes to mass deforestation and other environmental issues.
Paper manufacturers are investing in automation to meet consumer demand and improve productivity, while reducing waste and the negative environmental impact. However, manufacturers must be careful when increasing automation, as more equipment means more maintenance and more opportunities for breakdown.
Pulp and paper mills can be harsh environments for workers and machinery because they produce a lot of dust and heat. If manufacturers do not keep work areas clean and regularly inspect the machinery, it can break down with no warning which leads to expensive downtime for manufacturers.
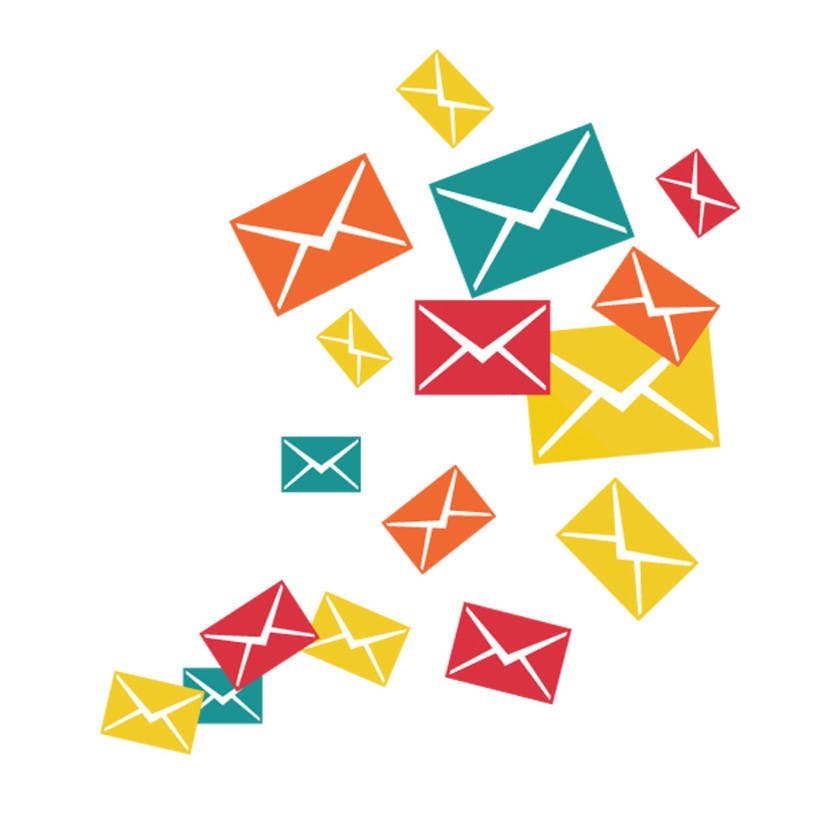
Paper manufacturers should consider how dust mitigation and regular machine inspections can help them prevent downtime. However, if a machine does break down without notice manufacturers do not need to panic.
This is where EU Automation can help out. We can locate the broken part that will bring manufacturers back to production, whether that part is new, reconditioned or no longer manufactured by the original equipment manufacturer (OEM). We specialise in sourcing obsolete parts and can offer a simple and effective repair service so that you save on parts and maintenance costs.
Our warehouse is stocked with all the major components a paper mill may require from a range of leading global suppliers. We can also guarantee worldwide delivery in 48 hours or less — helping you to get back to optimum production as quickly as possible.
Pulp and paper manufacturers must prioritise predictive maintenance in order to keep the mill running efficiently. Working with an obsolete industrial parts supplier means that manufacturers can return to production with minimal downtime and costs.
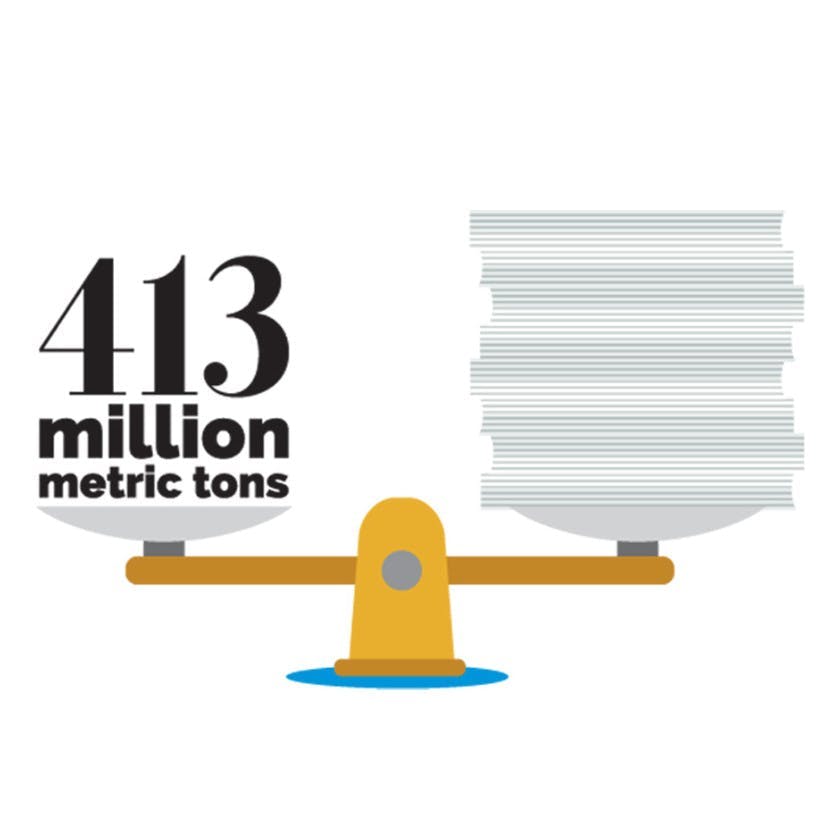
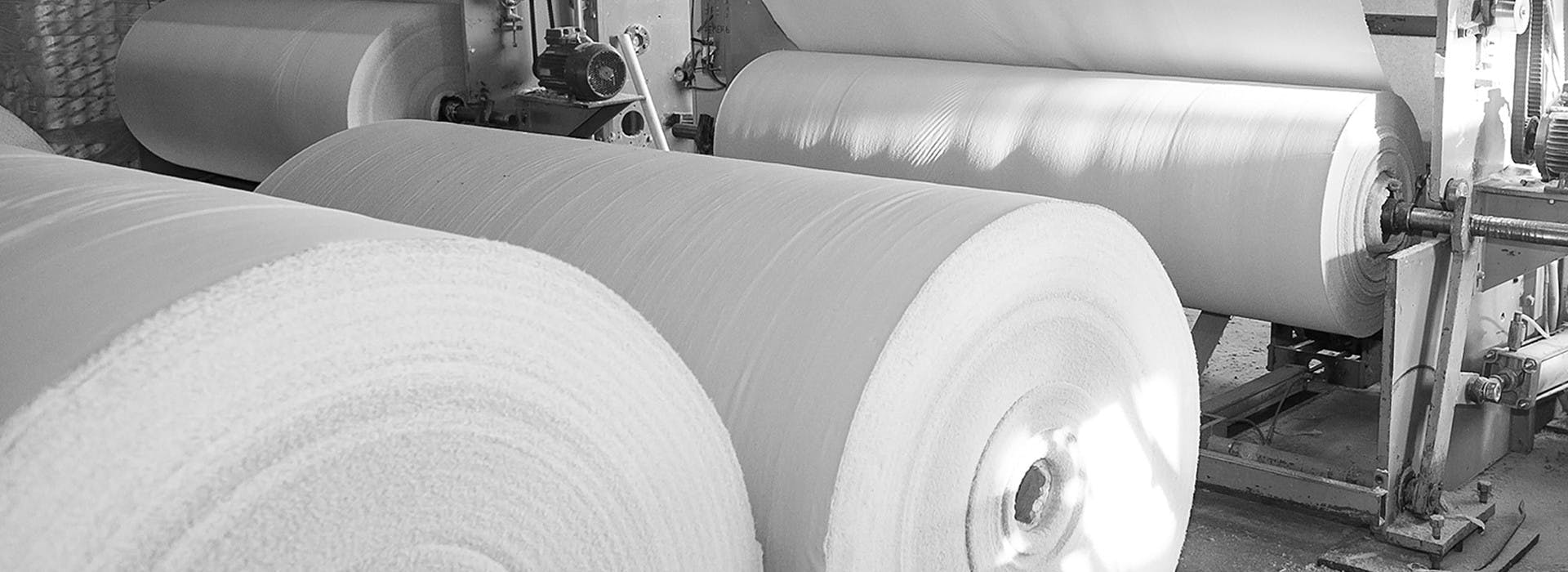
4. The future of paper, pulp and print
The pulp and paper industry has transformed with every industrial revolution. Manufacturers powered mills using steam, then electricity and have integrated automation and information technology to further improve productivity. Now, manufacturers need to take the steps to engage in the next phase — Industry 4.0. Here, we look at the technologies that will help manufacturers build the paper mill of the future.
Sensors
Paper production requires a lot of water and energy, which can be costly. Manufacturers can attach sensors to equipment, both to monitor machine condition and energy consumption in the facility.
Manufacturers can use sensors to see real-time information about machine condition. Maintenance teams can then detect potential breakdowns before they cause expensive downtime. They can also use collected data to find processes that use more energy than required and make changes to reduce energy costs.
Sustainable alternatives
The paper and pulp and the packaging industries are looking for new, more sustainable ways to produce paper and packaging materials. This is particularly important since governments across the world have focussed on reducing single-use plastics.
At the moment, manufacturers traditionally use either new wood or recycled paper for their products. However, they can also look to more sustainable fibrous products to help them reduce environmental impact.
For example, in 2016, a brewery in Florida produced edible beer pack rings for its products to reduce plastic pollution. They used the wheat and barley waste leftover from the brewing process to create a fibrous material strong enough to hold the cans. The packaging can safely be eaten, but if it does end up in the water, it will disintegrate in under two hours. Paper manufacturers should investigate the viability of using more sustainable materials in mass production to reduce negative environmental impact.
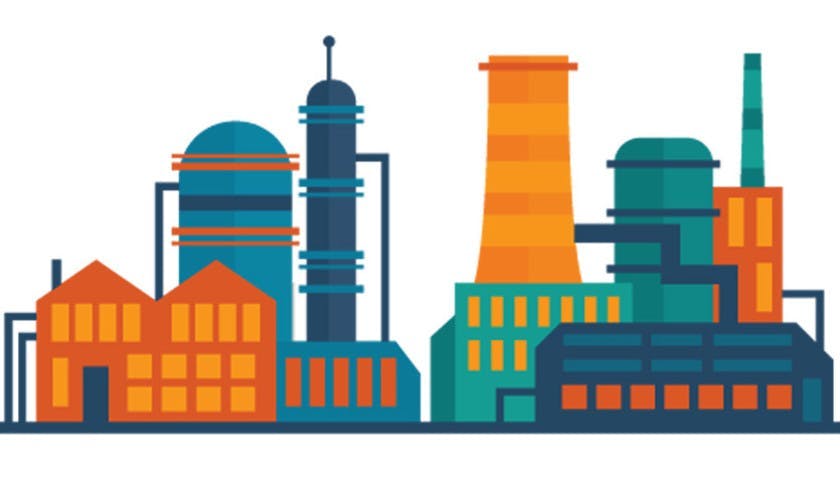
Smart packaging
Combining paper-based products and technology could change how we receive products in the future. Digital sensors in packaging can help customers receive products in a better condition. This can be either active packaging, with sensors that control the environment inside the packaging, that will be important for shipping food. Or there is intelligent packaging, where the technology will give consumers information about the product, such as its status.
Smart packaging will help manufacturers control products sent across the world and ensure customers will receive their items in perfect condition no matter where they are. However, manufacturers must consider how integrating technology into packaging will impact recycling and sustainability.
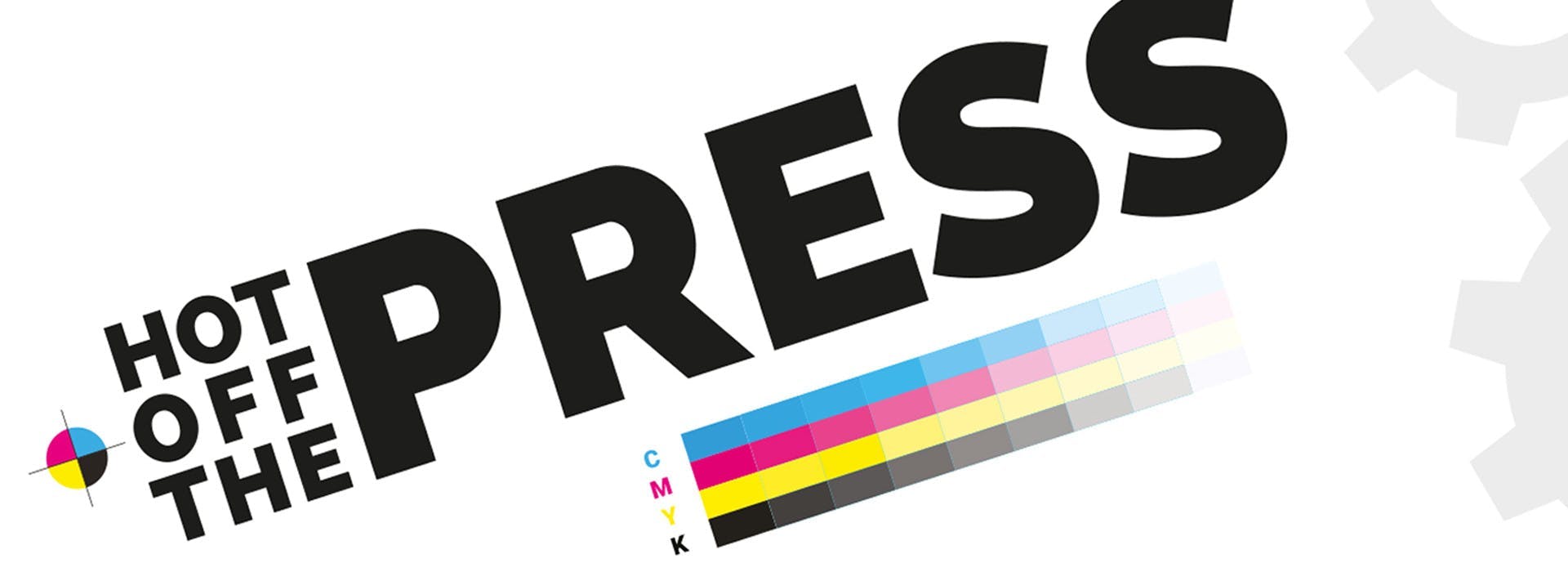
5. Hot off the press
The global pulp and paper industry accounts for four per cent of the world’s energy use, making it the fifth largest consumer of energy. As more automation is introduced to the market, paper manufacturers use this new automated technology to reduce energy consumption.
- You notice that your facility uses excessive amounts of energy to run
- You decide that you want to reduce energy costs — the best way to do this is to improve machine performance
- You invest in sensors to monitor your machines and these detect that your equipment is using more power than necessary
- You can buy equipment that will improve machine efficiency, such as variable speed drives (VSDs), that will control motor and conveyor speed
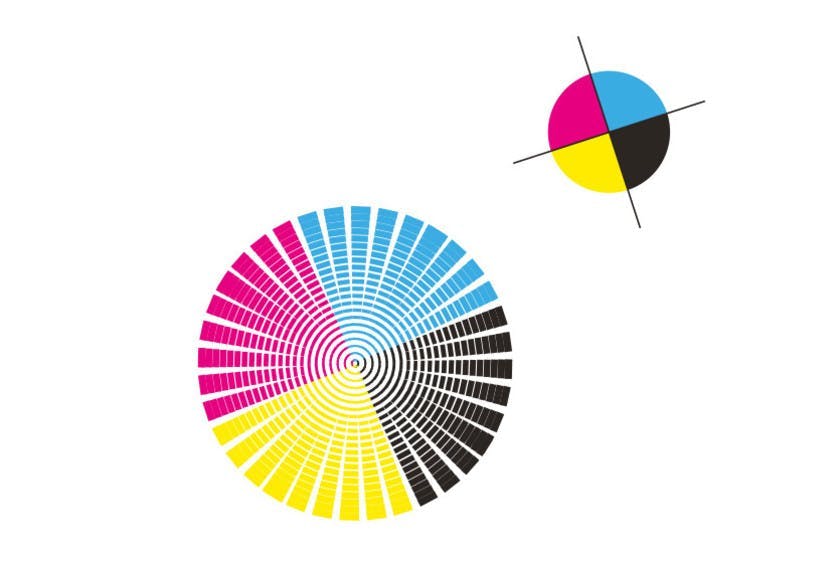
- At this point, you have to choose how you will purchase the new equipment. Purchasing completely new equipment can be expensive and may not be necessary.
- You can contact EU Automation. We stock obsolete and reconditioned parts that you can no longer buy from the original equipment manufacturer (OEM).
- Once you order the parts you need from our online catalogue, we can deliver them in under 48 hours, no matter where you are
- Installing the equipment helps you to monitor your machines more efficiently and you notice your energy consumption is reducing
- Now, you can continue to optimise machine performance and contact EU Automation to replace any parts that break down in the future
Improving machine performance allows your equipment work for longer with less risk of a breakdown.
더 많은 산업 살펴보기
Here to inspire you.
inspire
inspire
inspire
정기 업데이트 및 실제 자동화 인사이트를 이메일로 바로 받아보세요.