What is Condition-Based Maintenance?
2023-12-22
4 min read
In the ever-evolving landscape of industrial automation, maintaining the efficiency and reliability of machinery is paramount. You can use many different methods to optimise production and reduce downtime, but which one is best for you? This is where Condition-Based Maintenance (CBM) is proving its worth. It is a proactive strategy that has transformed maintenance protocols across industries.
CBM is very different from traditional methods of maintaining things. These strategies include reactive maintenance, which involves fixing equipment after it fails. In addition, it schedules maintenance based on the time intervals or usage intervals that are set. CBM takes advantage of recent advances in sensor technology. It also utilises data analytics and connectivity, including the Internet of Things (IoT), machine learning (ML), and Artificial Intelligence (AI). The goal is to provide a more efficient and cost-effective maintenance method.
The evolution of Condition-Based Maintenance
What is reactive maintenance?
‘If it isn’t broke, don’t fix it’ is an established maxim many industrial sites still use. However, there are other approaches to maintenance that can be taken. While this style of maintenance, termed “reactive maintenance”, has appeal, it also has large risks. Reactive maintenance does not require any upfront or ongoing costs and few, if any, dedicated personnel.
However, when machinery does break, the impact can be severe and often requires immediate attention. Several issues can arise from this situation, including limited human resources and significant delays in sourcing replacement parts. As well as, unexpected downtime costs that can amount to millions of dollars.
The simplest example would be the light bulb – it is only replaced when it blows. On the other hand, it is not a philosophy that scales well. The larger or more complex the equipment, the greater the consequence of it not working as it should. A Plant Engineering Maintenance Study indicated that 61% of manufacturing companies still used reactive maintenance for at least part of their operations.
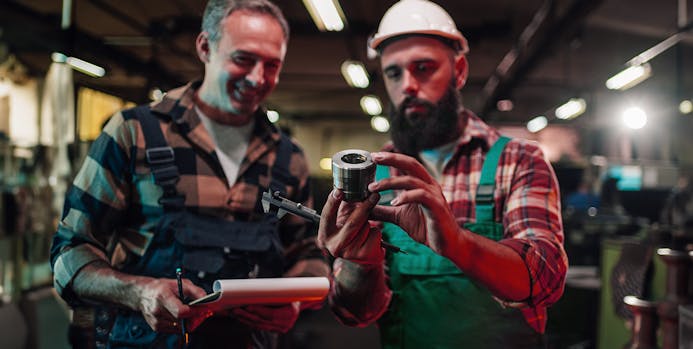
What is scheduled maintenance?
One way to minimise the chances of unplanned stoppages is to have a scheduled programme of equipment health monitoring. This also has the advantage of allowing a predictable budget and the appropriate staffing for maintenance operations.
A scheduled maintenance programme should be specific to an industrial site and all the equipment within it. You can build this programme using all assets' history data, including maintenance records, breakdown details, and running performance. This data can also come from the original equipment manufacturer (OEM) for new equipment. The chance of machine failure as well as the cost of maintenance and repairs will be reduced by this programme.
Good scheduled maintenance should be able to evolve as more information comes in. A pump that keeps breaking down due to leaking seals, bearing failure, or improper lubrication has not been maintained enough. As a result, the schedule should be tightened accordingly. This re-evaluation requires human instinct and input to update the schedule, while ongoing assessment can add structure.
What makes condition-based maintenance different?
Unplanned downtime characterises reactive maintenance. More often that not, it leads to higher overall costs due to emergency repairs and lost productivity. Scheduled maintenance, on the other hand, can notably result in unneeded maintenance. This leads to wasted resources and can be detrimental to the longevity of your equipment.
Condition-based maintenance involves the real-time monitoring of an asset. It provides specific indicators to help you to determine what maintenance you need to perform and when. With condition-based maintenance and real-time monitoring, engineers can avoid unnecessary production loss. They can have an up-to-the-minute assessment of equipment conditions through real-time monitoring and prior warning of failures.
When using sensors to measure vibration and temperature for equipment health monitoring, it becomes apparent when a machine is running normally. It also becomes apparent when it is not, and removes the need for unnecessary maintenance.
This revolution in condition-based maintenance has come about mainly through advances in sensors and connectivity. It is also enabled by the Internet of Things (IoT) and is increasingly improving due to machine learning (ML) and Artificial Intelligence (AI).
Overall, CBM offers a more efficient and cost-effective maintenance strategy by using technology to monitor and predict equipment needs.