Unlocking the accuracy of condition-based maintenance
2024-01-16
2 min read
Preventative maintenance relies on the accuracy of historical data. On the other hand, predictive maintenance uses live machine health monitoring data to determine when an asset needs to be maintained or replaced. This is where condition-based maintenance with real-time monitoring comes in.
Sensor and connectivity technology advances have made it feasible to collect real-time data from every asset. Analysing the data and comparing it to historical and expected performance can reveal whether a machine operates normally or drifts towards its performance limits. Using this information for equipment health monitoring, corrective condition-based maintenance can be planned before the machine fails and also at a time when it suits maintenance staff and factory/production schedules. It also means that equipment is not taken out of operation for maintenance more often than is required – scheduled maintenance is often unnecessary. Perversely, over-maintained machines can age more quickly than optimally maintained ones; for example, adding grease to a sufficiently lubricated part just because of the schedule can reduce machine efficiency and increase contamination.
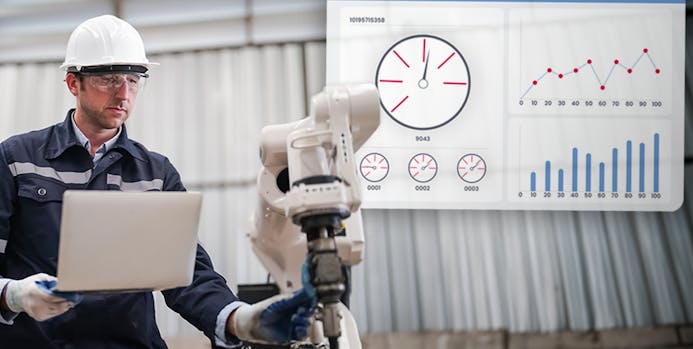
The maintenance sweet spot
Condition-based maintenance being largely, although not exclusively, a real-time monitoring and continuous machine health monitoring tool, enables the identification of potential problems close to when machine performance begins to drop. It thus provides the longest maintenance window and more flexibility around scheduling the necessary downtime. Typically, the cost of repairing a machine rises as its condition deteriorates; the closer that a fault is detected to the point of potential failure, the cheaper the maintenance or repair will be. Waiting until the optimal time to perform repairs and maintenance prevents the unnecessary cost and time involved in maintaining that asset under scheduled or preventative maintenance methodologies.
Catching potential problems early benefits factory uptime, the biggest advantage of condition-based maintenance, and streamlines maintenance costs and staffing activities. It also improves asset longevity, can make the factory safer, and even has beneficial consequences for product quality and customer satisfaction. In terms of the benefits of condition-based monitoring, McKinsey anecdotally takes the example of a large technology manufacturer that introduced a condition-based maintenance framework pulling data from several different sources, including Industrial IoT (IIoT) devices and a historical service database. The consequent savings in reduced labour, downtime, parts, and other related costs were around 30%.
Condition-based maintenance in action
The primary benefits of condition-based maintenance have been outlined by some of the world’s leading technology companies. Research and data from IBM in development of its Maximo intelligent asset management suite has led to it citing five tangible benefits that are applicable across manufacturing organisations:
- Prevention of equipment failures and downtime.
- Extension of asset lifespan.
- Improved safety through enhanced issue detection.
- Reduced maintenance costs.
- Improved maintenance efficiency.
IBM suggests that the combined benefits are substantial: it says that condition-based and predictive maintenance alone can reduce costs by 15% – 20% and improve asset availability by 20%.