Lecciones aprendidas de la automatización del espacio profundo
2021-08-31
3 min read
En octubre de 2020, la sonda espacial OSIRIS-REx de la NASA bajó de la órbita alrededor del asteroide 101955 Bennu y obtuvo una muestra de la superficie del asteroide. Con su vuelta en 2023, el objetivo de la misión es ayudar a los científicos a conocer la formación y evolución del sistema solar a partir de la configuración química de la muestra.
Entre las sondas espaciales, OSIRIS-REx tiene una característica especialmente interesante: el mecanismo de adquisición de muestras de solo un toque (TAGSAM), un brazo robótico accionado eléctricamente de 3,35 metros de longitud con tres articulaciones articuladas y un aparato de recogida de muestras en un extremo. El brazo está diseñado para una serie de movimientos, como por ejemplo, su extensión completa durante la toma de muestras, así como otras posiciones necesarias para la verificación visual de muestras y el almacenaje seguro.
Lo que lo hace tan impresionante es que tiene que trabajar de forma totalmente autónoma. Bennu está a más de tres horas luz, lo que hace imposible el control manual, ya que cada entrada necesita al menos seis horas para hacer el viaje de ida y vuelta. Cada función, desde el control del propulsor hasta la orientación y el vector de la nave espacial, pasando por las distintas posiciones del TAGSAM, debe ser programada previamente por los equipos en tierra de la NASA. Cualquier acción que requiera una reacción más rápida de seis horas deberá programarse en su lógica integrada.
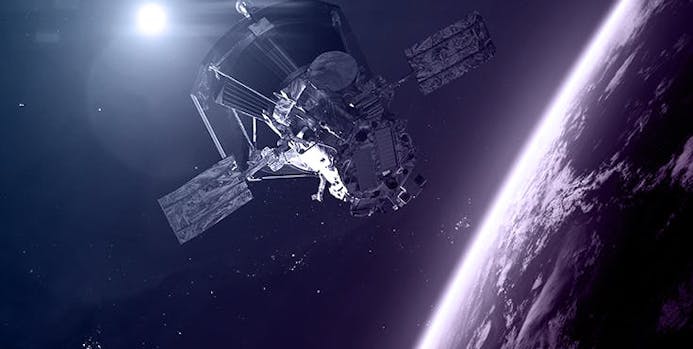
El TAGSAM autónomo muestra claras similitudes con los brazos robóticos que se encuentran en las instalaciones de fabricación. FANUC, por ejemplo, produce una amplia gama de robótica, desde recolectores de 6 ejes hasta robots CNC lineales, muchos de los cuales pueden funcionar de forma autónoma en instalaciones automatizadas, de forma muy parecida a como lo hace el TAGSAM en el espacio.
Una llamada de mantenimiento de (muy) larga distancia
Debido a la inaccesibilidad del TAGSAM, el mantenimiento es imposible, aunque el fallo de un componente podría significar el fracaso de toda la misión. Por lo tanto, la sonda debe funcionar sin mantenimiento y en condiciones extremas durante varios años mientras se realiza la misión. A fin de eliminar el requisito del mantenimiento, la NASA trabajó arduamente para producir un diseño adecuado y lograr la calidad de fabricación requerida. Incluso entonces, la NASA incluyó conjuntos redundantes de actuadores y sensores de posición para reducir aún más el riesgo.
La diferencia evidente es que, en la Tierra, sí es posible el mantenimiento. De hecho, se trata de una actividad cotidiana. Para los fabricantes que utilizan equipos de automatización, la posibilidad de que una máquina se averíe es una realidad. Por eso, podemos aprender mucho del enfoque «sin mantenimiento a toda costa» de la NASA.
Sigue siendo habitual comprar equipos y tenerlos en funcionamiento hasta que se produzca un fallo. Sin embargo, las nuevas tecnologías ahora nos permiten añadir sensores tanto a los equipos nuevos como a los antiguos para conocer su rendimiento. Por ejemplo, un sensor inteligente conectado a un motor puede alertar a los directores de producción si el motor se calienta demasiado, a fin de que puedan detener la producción y comprobar su estado. Un paso más allá de esa solución encontramos un enfoque más global, que recopila datos de sensores conectados en una plataforma central y utiliza software de análisis predictivo para detectar cualquier posible problema en las instalaciones.
Estos enfoques proactivos permiten a los fabricantes limitar los tiempos de inactividad: en lugar de que los tiempos de inactividad imprevistos se prolonguen por retrasos debido a la sustitución de piezas, los fabricantes pueden simplemente pedir el componente para su entrega y planificar algunas reparaciones rápidas antes de que su línea deje de funcionar. Aunque nuestras líneas de fabricación están muy lejos de las de la NASA y OSIRIS-REx, tomar medidas para reducir el mantenimiento y no abortar una misión es la mejor técnica posible.
En EU Automation sabemos que el tiempo es crucial cuando la producción se detiene, razón por la cual podemos entregar cualquiera de los millones de piezas de alta calidad de nuestro catálogo en cualquier parte del planeta en 72 horas, o 24 horas en el caso de Europa.