Robots industriels : limites et solutions
2023-06-20
4 min read
Aujourd'hui, les robots industriels sont utilisés dans presque tous les secteurs, de l'automobile aux plastiques en passant par les technologies médicales. Ils apportent de nombreux avantages aux sites de fabrication et ouvrent la voie aux usines intelligentes du futur. Néanmoins, certaines limites doivent être prises en compte par les fabricants lors du choix de leur équipement robotique.
Selon Fortune Business Insights, la demande en processus automatisés augmente et le marché des robots industriels devrait atteindre 31,3 milliards de dollars en 2028. Les fabricants reconnaissant les avantages potentiels du déploiement de robots dans leurs opérations, il est essentiel de reconnaître les limites associées à ces machines. Dans ce blog, nous étudierons trois principales limites des robots industriels (accessibilité, sécurité et entraînement) et nous apporterons des informations sur la manière dont les fabricants peuvent surmonter ces difficultés.
Accessibilité
Les robots industriels nécessitent souvent un investissement initial important, notamment les coûts d'installation et de configuration. De plus, les fabricants doivent prendre en compte les frais de maintenance récurrents et le besoin de composants supplémentaires.
De même, la robotique est un secteur en constante évolution, de nouvelles machines apparaissant constamment sur le marché. Investir régulièrement dans de nouveaux robots pourrait être une difficulté pour certaines entreprises, en particulier les plus petites qui pourraient faire faillite dans leur tentative de suivre les tendances industrielles.
Cependant, les robots industriels peuvent aider les fabricants à réduire les coûts dans différents domaines. Ils peuvent réduire les coûts de production et augmenter les bénéfices en optimisant le travail. Avec une stratégie d'investissement et un plan financier clairs, les robots sont les plus susceptibles d'apporter un retour sur investissement rapide. Investir dans des robots reconditionnés est une alternative rentable. Ils offrent une efficacité et une opérabilité similaires à une fraction du coût des robots neufs.
Sécurité
Les robots industriels ont toujours été considérés comme dangereux dans les usines. Et pour une bonne raison : il s'agit de gros équipements massifs qui peuvent se déplacer à des vitesses très élevées. Les machines plus anciennes ne disposent même pas des capacités sensorielles nécessaires pour détecter les humains à proximité, ce qui les rend vulnérables aux collisions et aux accidents dangereux. Pour cette raison, de nombreux fabricants ajoutent des cages ou des cloisons pour séparer les robots de leurs collaborateurs humains.
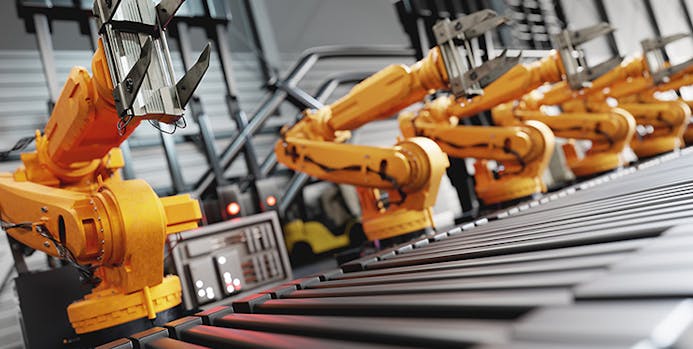
Cependant, les progrès technologiques ont conduit à l'émergence de robots collaboratifs (cobots) spécialement conçus pour travailler en toute sécurité aux côtés des humains. Des pratiques réglementaires ont également été mises en œuvre pour améliorer la sécurité des robots industriels traditionnels et des cobots.
Même si la sécurité absolue n'est pas encore atteinte, les progrès continus tels que les rideaux lumineux, les scanners laser et les dispositifs de détection de présence sont largement adoptés comme des méthodes efficaces pour améliorer la sécurité humaine. En outre, effectuer des évaluations individuelles des risques des lignes de production et fournir une formation complète aux travailleurs sur la manière de réagir en cas d'accidents potentiels peut améliorer davantage la sécurité sur le lieu de travail.
Plus difficile à former
Les robots industriels nécessitent une programmation et une formation spécialisées, nécessitant le recrutement d'ingénieurs et de programmeurs expérimentés pendant l'installation. Même un personnel expérimenté peut avoir besoin de recevoir une nouvelle formation lorsque de nouveaux logiciels ou de nouveaux modèles de robots entrent sur le marché. Une mauvaise programmation peut entraîner des dysfonctionnements et présenter des risques pour ceux qui travaillent à proximité.
Cependant, ces dernières années, une nouvelle méthode de formation des robots a été mise en œuvre : la programmation No-code ou Low-code. Elle permet aux employés ayant moins d'expérience en codage de configurer un robot à l'aide de la modélisation visuelle et d'interfaces utilisateur par glisser-déposer. En raison du format simple à utiliser des plateformes No-code et Low-code, les robots peuvent être reprogrammés facilement pour différentes tâches en ajustant leur bras. Alors que les entreprises avaient autrefois besoin de plusieurs robots, un simple ajustement peut désormais être effectué par une personne sans compétences techniques, ce qui permet aux entreprises de gagner du temps, de l'espace et de l'argent.
La tendance des plateformes Low-code et No-code est en hausse. 84 % des entreprises aux États-Unis, au Royaume-Uni, au Canada et en Australie mettent en œuvre des plateformes de développement Low-code pour réduire les besoins de codage.
Les robots industriels offrent sans aucun doute des avantages significatifs, en rationalisant la production et en fournissant un retour sur investissement rapide aux fabricants. Cependant, il est essentiel de remédier de manière proactive à leurs limites. En mettant en œuvre une planification efficace, en explorant des options de réduction des coûts, en hiérarchisant les mesures de sécurité et en adoptant de nouvelles technologies de formation, les fabricants peuvent surmonter les défis associés aux robots industriels et exploiter pleinement leur potentiel dans la construction d'usines intelligentes du futur.
Si vous souhaitez rester informé des progrès de la robotique industrielle, rendez-vous sur le site www.euautomation.com.