Une maintenance conditionnelle plus précise
2024-01-16
4 min read
La maintenance préventive repose sur l'exactitude des données historiques. En revanche, la maintenance prédictive utilise les données de surveillance de l'état des machines en temps réel pour déterminer quand un actif doit être entretenu ou remplacé. C'est là qu'intervient la maintenance conditionnelle avec surveillance en temps réel.
Les progrès de la technologie des capteurs et de la connectivité ont rendu possible la collecte de données en temps réel de chaque actif. L'analyse des données et leur comparaison avec les performances historiques et attendues permettent de déterminer si une machine fonctionne normalement ou si elle se rapproche de ses limites de performance. En utilisant ces informations pour surveiller l'état de l'équipement, la maintenance conditionnelle peut être planifiée avant que la machine ne tombe en panne et à un moment qui convient au personnel de maintenance et aux calendriers d'usine/de production. Cela signifie également que l'équipement n'est pas mis hors service pour maintenance plus souvent que nécessaire, car la maintenance programmée est souvent inutile. Paradoxalement, les machines sur-entretenues peuvent vieillir plus rapidement que celles entretenues de manière optimale ; par exemple, le fait d'ajouter de la graisse à une pièce suffisamment lubrifiée uniquement en raison du calendrier peut réduire l'efficacité de la machine et augmenter la contamination.
La fréquence de maintenance optimale
La maintenance conditionnelle étant en grande partie, mais pas exclusivement, un outil de surveillance en temps réel et de surveillance continue de l'état des machines, elle permet d'identifier les problèmes potentiels peu de temps avant que les performances de la machine ne commencent à diminuer. Elle offre ainsi la plus longue fenêtre de maintenance et une plus grande flexibilité pour planifier les temps d'arrêt nécessaires. En règle générale, le coût de réparation d'une machine augmente au fur et à mesure que son état se détériore ; plus un défaut est détecté près du point de défaillance potentielle, moins la maintenance ou la réparation sera coûteuse. Attendre le moment optimal pour effectuer les réparations et la maintenance permet d'éviter les coûts et les délais inutiles liés à l'entretien de l'actif dans le cadre de méthodologies de maintenance programmée ou préventive.
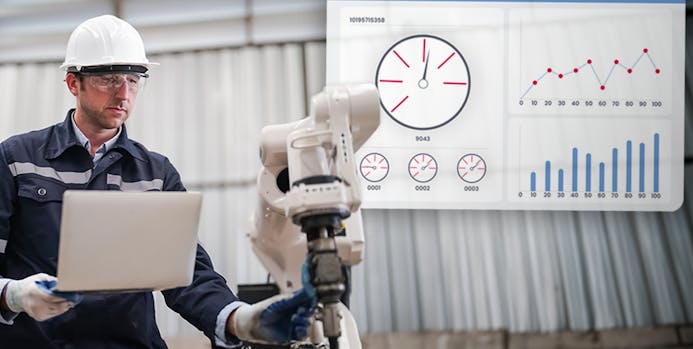
La fréquence de maintenance optimale
La maintenance conditionnelle étant en grande partie, mais pas exclusivement, un outil de surveillance en temps réel et de surveillance continue de l'état des machines, elle permet d'identifier les problèmes potentiels peu de temps avant que les performances de la machine ne commencent à diminuer. Elle offre ainsi la plus longue fenêtre de maintenance et une plus grande flexibilité pour planifier les temps d'arrêt nécessaires. En règle générale, le coût de réparation d'une machine augmente au fur et à mesure que son état se détériore ; plus un défaut est détecté près du point de défaillance potentielle, moins la maintenance ou la réparation sera coûteuse. Attendre le moment optimal pour effectuer les réparations et la maintenance permet d'éviter les coûts et les délais inutiles liés à l'entretien de l'actif dans le cadre de méthodologies de maintenance programmée ou préventive.
La détection précoce des problèmes potentiels améliore le temps de fonctionnement de l'usine, ce qui constitue le principal avantage de la maintenance conditionnelle, et permet de rationaliser les coûts de maintenance et les activités des effectifs. Elle améliore également la longévité des actifs, peut rendre l'usine plus sûre et a même des conséquences bénéfiques sur la qualité des produits et la satisfaction des clients. En ce qui concerne les avantages de la surveillance conditionnelle, McKinsey prend l'exemple d'un grand fabricant de technologies qui a introduit un cadre de maintenance conditionnelle tirant des données de plusieurs sources différentes, y compris des dispositifs IoT industriels (IIoT) et une base de données de services historiques. Les économies conséquentes en termes de réduction de la main-d'œuvre, des temps d'arrêt, des pièces et d'autres coûts connexes étaient d'environ 30 %.
La maintenance conditionnelle en action
Les principaux avantages de la maintenance conditionnelle ont été soulignés par certaines des plus grandes entreprises technologiques du monde. Les recherches et les données d'IBM lors du développement de sa suite de gestion intelligente des actifs Maximo lui ont permis de citer cinq avantages tangibles applicables à l'ensemble des entreprises manufacturières :
- Prévention des défaillances d'équipement et des temps d'arrêt.
- Prolongation de la durée de vie des actifs.
- Amélioration de la sécurité grâce à une meilleure détection des problèmes.
- Diminution des coûts de maintenance.
- Amélioration de l'efficacité de la maintenance.
Selon IBM, les avantages combinés sont substantiels : la maintenance conditionnelle et prédictive peut à elle seule réduire les coûts de 15 % à 20 % et améliorer la disponibilité des actifs de 20 %.