Winter shutdowns in manufacturing: Is it worth it?
2024-11-06
4 min read
Winter is coming—along with tough decisions for engineers and technicians on the front lines of manufacturing. As temperatures drop, some facilities prepare for winter shutdowns in manufacturing. They aim to carry out essential maintenance, which helps conserve energy. It also gives equipment a breather.
However, in certain industries, production is continuous. This includes sectors like food, pharmaceuticals, and consumer goods. Therefore, a seasonal shutdown may not be feasible.
Navigating the challenges of winter production is key to keeping operations efficient and avoiding costly setbacks. Therefore, what is your strategy for the upcoming season? Let’s explore how you can make the most of winter production, whether your facility is winding down or forging ahead.
Benefits of winter shutdowns in manufacturing
1) Essential repairs and maintenance during holiday shutdown
Winter shutdowns in manufacturing provide the perfect window for preventive maintenance and critical system upgrades. These are difficult to manage during regular operations. For industries like automotive and aerospace, this break allows facilities to carry out essential inspections, winter maintenance, and repairs. Therefore, preventing costly breakdowns and unplanned downtime later in the year. In fact, a study by Deloitte shows that facilities with preventive maintenance programs reduce downtime by 30% and repair costs by 40%. [1]
2) Energy and cost savings
Shutting down operations can significantly reduce energy consumption during the coldest months, especially in energy-intensive industries. The U.S. Department of Energy states that manufacturing facilities have the potential to cut energy costs. This reduction can be as much as 20% [2], during a well-planned winter shutdown. This not only lowers costs but also aligns with sustainability goals. Reduced energy use decreases the carbon footprint during a period of high demand.
3) Employee rest and training
Shutting down over the winter holidays gives you and your team a chance to recharge. This allows your employees to come back feeling more energised for the challenges ahead. It’s a great time to improve your technical skills.
You can also address any pending maintenance task and consider reorganising your workflows. These efforts can help streamline daily operations. They ensure everything’s in top shape and ready to hit the ground running in the new year.
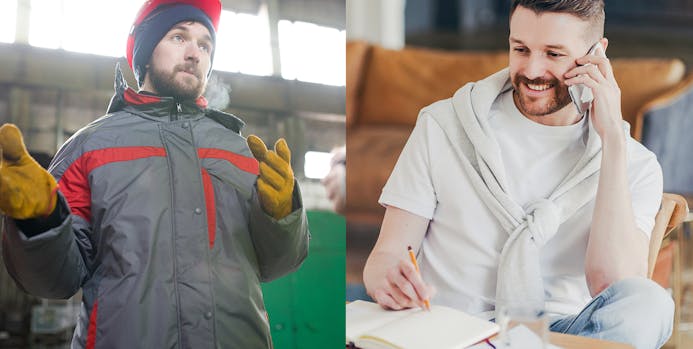
Challenges of winter shutdowns in manufacturing
1) Continuous production needs
For industries like food and pharmaceuticals, pausing production is not an option. These industries require continuous operation to maintain product quality and meet strict supply chain timelines. Shutting down could lead to spoilage or disrupt market supply, posing greater risks than the potential benefits of downtime.
2) High-demand periods
Manufacturers of consumer goods often see a surge in production during winter. This is especially true for those in electronics and packaging materials. The holiday season drives this peak production period. A shutdown during this time would lead to missed opportunities and potentially delayed orders, damaging customer relationships and revenue.
3) Restart costs and disruptions
Small and medium-sized businesses may struggle to absorb the costs of downtime. Restarting production after a shutdown can be expensive, requiring recalibration and testing of equipment. This can delay full production capacity. Lost revenue during this period may also outweigh any savings gained from a temporary halt.
4) Industry trends and size considerations
Larger manufacturers often prefer winter shutdowns. This is especially true in industries such as automotive and heavy machinery. They tend to favour seasonal shutdowns due to the scale and complexity of their equipment.
Medium-sized companies might take a more flexible approach, opting for shorter shutdown periods or partial operations. Meanwhile, smaller companies often find it more practical to conduct maintenance during off-hours. This approach helps them to avoid the financial burden of a complete pause.
Conclusion
Deciding whether to implement a winter shutdown in manufacturing depends on your industry, geographic location, and company size. Some sectors benefit from the opportunity to reset as they can save on energy costs. However, others face challenges, especially those with high winter demand or continuous production needs. For them, the risks may outweigh the rewards.
Whether you’re shutting down for the winter or in the thick of seasonal demand, EU Automation is your trusted partner. We provide fast, reliable access to a global supply of automation parts and components. Therefore, we ensure minimal downtime and maximum efficiency.
Our dedicated account managers and expert support team are available around the clock. Together, they offer rapid delivery and guidance, ensuring you stay on track, no matter the season.