- Início >
- Indústrias >
- Energia >
-
Industry Report
Energia
An industry that has been around for hundreds of years and that employs hundreds of thousands of people across the globe. The chemical industry shows no signs of slowing down and is only gaining traction. But for how much longer? We explore the past and future of the chemicals industry and whether or not it is sustainable in our in-depth industry report.
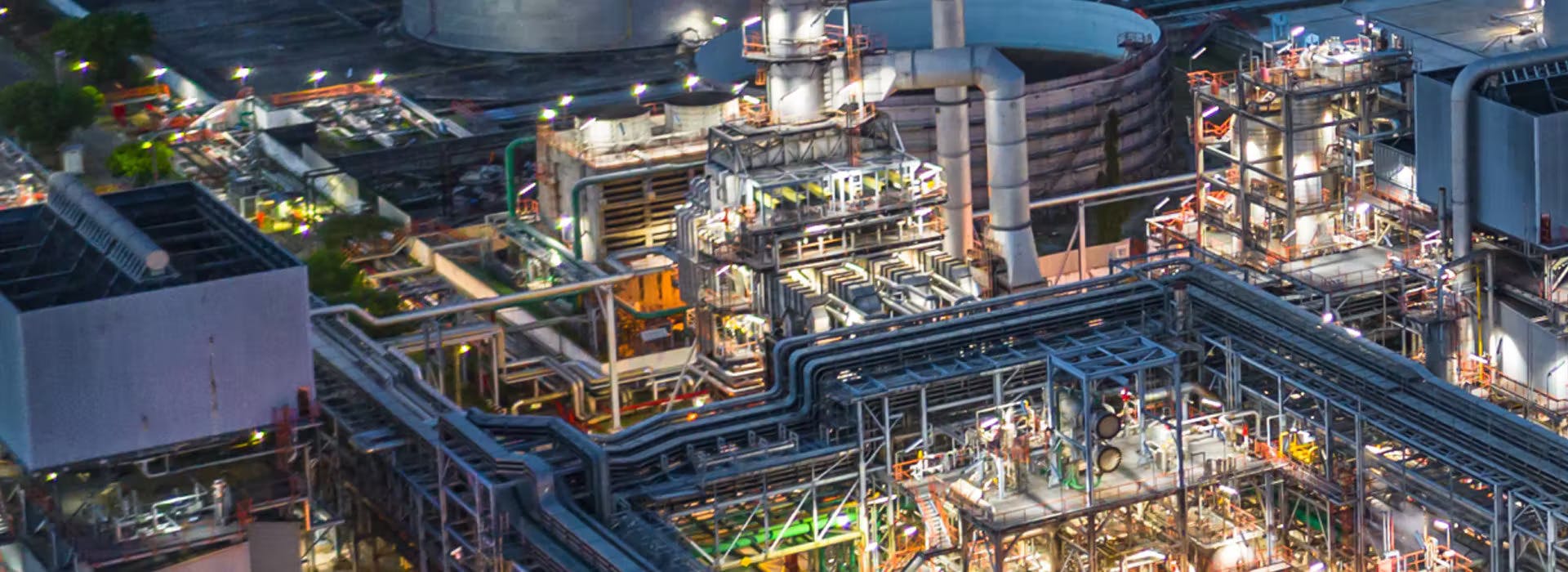
1. Insight into chemical production
An industry that has been around for hundreds of years and that employs hundreds of thousands of people across the globe. The chemical industry shows no signs of slowing down and is only gaining traction. But for how much longer? Here, Jonathan Wilkins, marketing director at obsolete parts specialist, EU Automation, explores the past and future of the chemicals industry and whether or not it is sustainable.
The chemical industry is a complex yet profitable industry. Although it has been in existence for many years, the real surge for the industry came during the industrial revolution. In the 18th century, the industry began taking shape and by the 19th century, it had grown into a monumental and history-changing industry.
Today, the chemical industry remains huge and unwavering and in the US alone, it is worth over $750 billion a year. But how sustainable is the industry? Can our planet keep up with the demands and pressures we are putting on it?
The strain that the chemical industry is putting on the environment is unquestionable and alarming. That’s not to say that the eradication of these industries is even possible or would solve the problems we are facing across the globe, but steps must be taken to make the industry more sustainable.
There are two portions of the industry which are of particular concern; coal and petroleum. When we look at their past and roles in industry it is easy to see why we rely so heavily on them for multiple resources. However, this cannot and will not last forever, so as we look towards the future of these industries, what do we see and how do we improve the sustainability of them for future generations and for the planet?
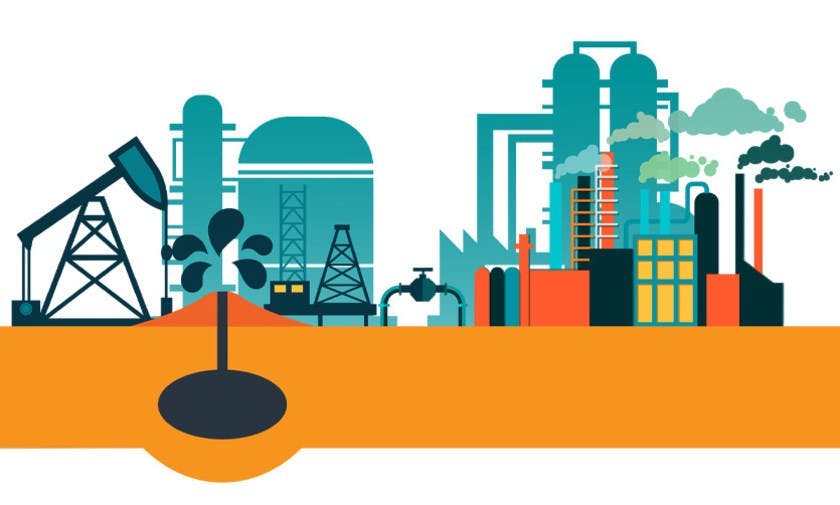
The conundrum with coal
Coal is one of the oldest materials in the modern world and has been in popular use since the 1880s. It is valued for its characteristics and used in a variety of applications. However, it wasn’t until the early 1900s that machinery took over the manual tasks of extracting coal from the ground, revolutionising the industry and improving the health of coal workers.
The problem with coal is that it is a finite source of energy. It is not renewable and therefore poses the question of whether or not it is sustainable. When the day comes where coal is not longer a viable option, what methods will we turn to, to achieve the same or similar results we see from coal?
Natural gas is a viable replacement for coal which would solve a lot of the issues associated with the mining and extraction of coal. Biomas is a second sustainable replacement for coal, readily available and a constant replenishment of the product. A third option would be nuclear power which again boasts benefits over coal such as low pollution levels and high energy density.
The problem with petroleum
Similarly to coal, petroleum is a substance that we use on a daily basis and rely heavily on. The industry includes the exploration, extraction, refining and transporting of the oil which in turn creates a profitable industry and many jobs for human workers. While it is a naturally occurring liquid, the rate we mine and use it means that it will not last forever. For years we have abused the sources available to us which will leave us in a tricky situation when it does eventually run out.
This problem may come sooner than we think. This is why we must find ways to replace petrol where we can with more sustainable solutions. These could include bio-diesel which would derive from waste which will always be available or chemically stored electricity which again could become a renewable source of energy.
The solutions to sustainability will come from building alternative sources into the energy mix and chemical production systems. While we will never eradicate the pollution levels and the rate we are burning though these products, we can certainly introduce alternatives and make more conscious decisions when it comes to chemical production.
In an industry that has been around for hundreds of years, it will be interesting to see where it is heading next and what changes are introduced to make the industry one that is more sustainable and will offer a better future for the planet and the generations to come. Over the next ten to 20 years, we predict a lot of change and new materials being introduced to the industry that could revolutionise and alter chemical manufacturing and production drastically. Our eyes are peeled and we are ready to welcome in these changes.
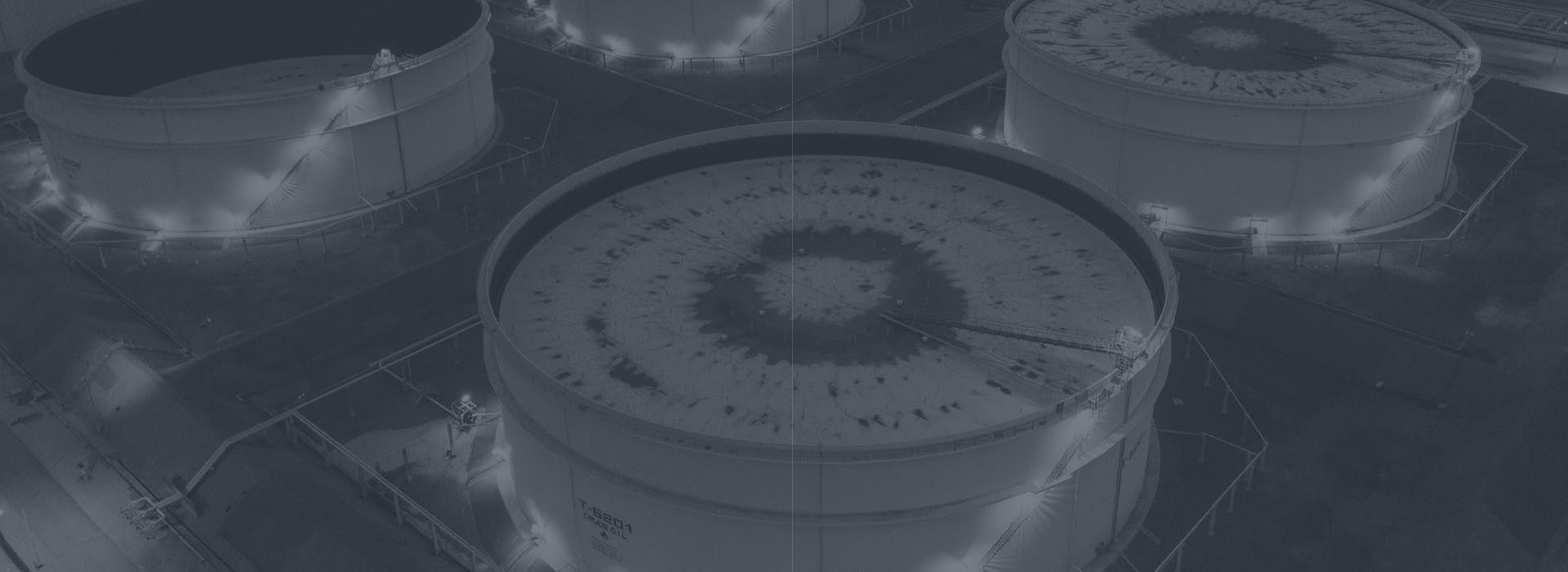
2. The future of fuel
Three technologies changing the petroleum and coal industry
In the 19th century, mining for coal involved a stick of dynamite, a pick axe and maybe even a canary ─ the fuel industry has dramatically changed since then. Despite increasing efforts to produce greener, more sustainable energy, there are several new and innovative technologies paving the way for a smarter, more efficient future of fuel.
According to the Financial Times, by 2025 advancements in the exploration and production of fuel could save the industry $75 billion per year. By adopting new technologies, businesses in the petroleum industry can maintain their position in a competitive market.
Smart drilling
It has become common practice that drilling is about reaching oil as quickly as possible, regardless of exactly how you get there. However, the integration of smart technology has led to more firms opting for an advanced planning procedure before diving straight in.
Traditionally, only one in three exploration wells found usable volumes of oil and gas, however using Real-Time Drilling Advisory Systems and advanced reservoir models has optimised this process exponentially. Using data driven, physics-based calculations these systems show more sophisticated maps of the rocks and fluids below ground for more accurate drilling.
Automation
The fuel industry certainly isn’t the first to implement automation, as it increases productivity, efficiency and safety across a range of industries.
Norwegian energy company Equinor has released the first fully automated offshore oil and gas platform. The Oseberg H, located in the North Sea, cost approximately £606 million to build and due to its fully automated status, has no toilets, beds, or any human facilities at all. While the rig does require a couple of maintenance visits a year, it remains fully functional while completely unmanned.
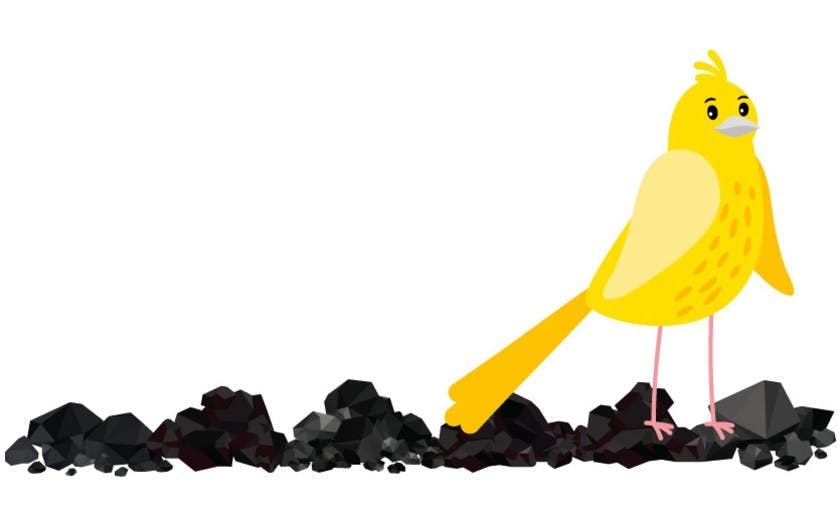
Connected oilfields
Oil and gas companies often operate from multiple sites in a broad geographic area. Keeping all these sites connected with each other, and the rig itself, is a major advantage.
By using real-time data surveillance, companies can identify and analyse issues remotely with the use of a headset and a tablet. To enable this, intelligent sensors can be fitted to machinery to collect huge amounts of real-time data. The operator can then send commands remotely, to adjust the performance of equipment.
We no longer use canaries or dynamite when mining for fuel. Instead, the industry is turning to more intelligent technology that helps to improve productivity, efficiency and safety.
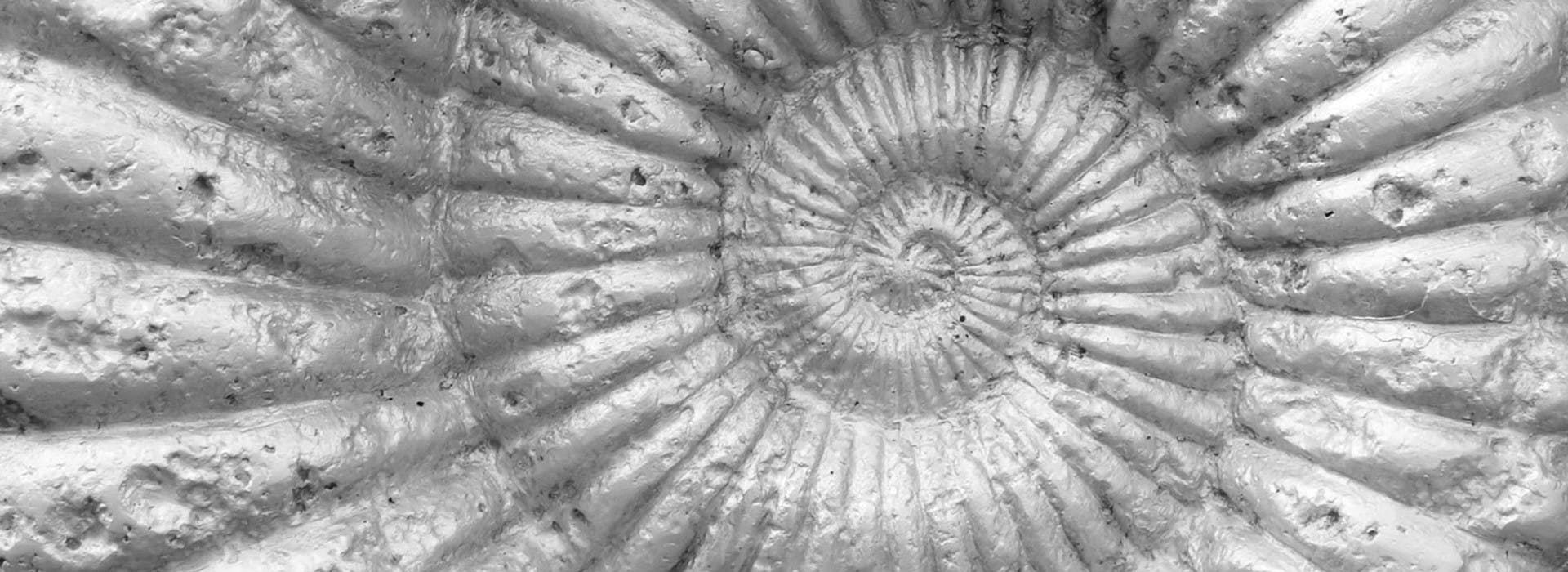
3. Oil, gas & coal – How our services work for you
The safety of humans and the environment are primary concerns in the extraction and refinement of fossil fuels. To help protect the health of their employees, many decision makers in this sector are now dealing with safety issues by automating processes that used to be carried on manually. As a consequence, the use of automated machinery and other control systems is becoming commonplace in the industry.
Automation has provided many advantages to this sector, the most important being increased productivity and reduced health and safety hazards. However, manufacturers must be careful when increasing automation, as more equipment means more maintenance and more opportunities for breakdown.
Additionally, the oil, gas and coal industry is a highly regulated field, so when equipment breaks it can be difficult to purchase and install new machinery that complies with current regulations. In this case, repairing the existing equipment can often be the best solution.
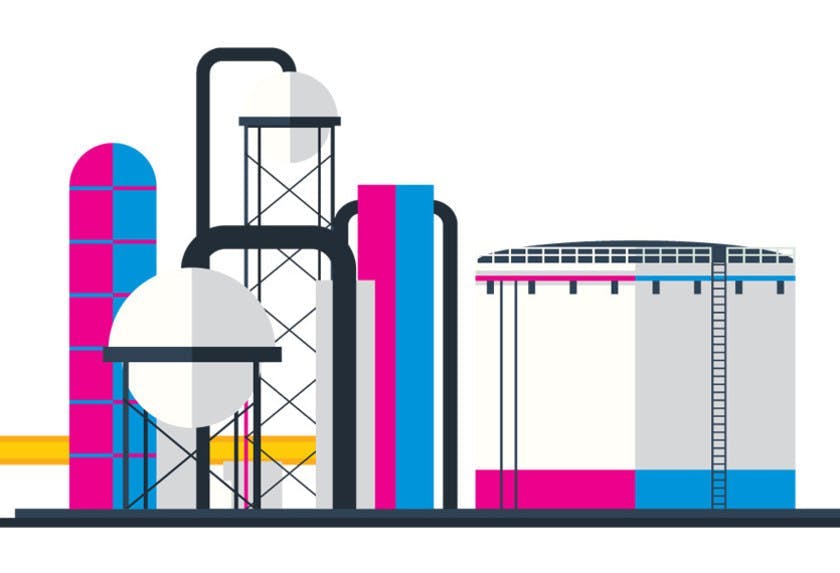
A reliable industrial automation parts supplier like EU Automation can help you in this phase. We can locate the broken part that will bring your extraction plant back to production, regardless of whether that part is new, reconditioned or no longer manufactured by the original equipment manufacturer (OEM). We specialise in sourcing obsolete parts and can offer a simple, fast and cost- effective repair service so that you save on parts and maintenance costs.
Our warehouses are stocked with many of the major components an extraction and refinement plant may require, which we source from a range of leading global suppliers. We can also guarantee same day international dispatch — helping you to get back to optimum production as quickly as possible.
Plant managers must prioritise predictive maintenance in order to keep their plants running efficiently and, most importantly, safely. Working with a trustworthy industrial parts supplier means that you can minimise safety risks and return to production with minimal downtime and maintenance costs.
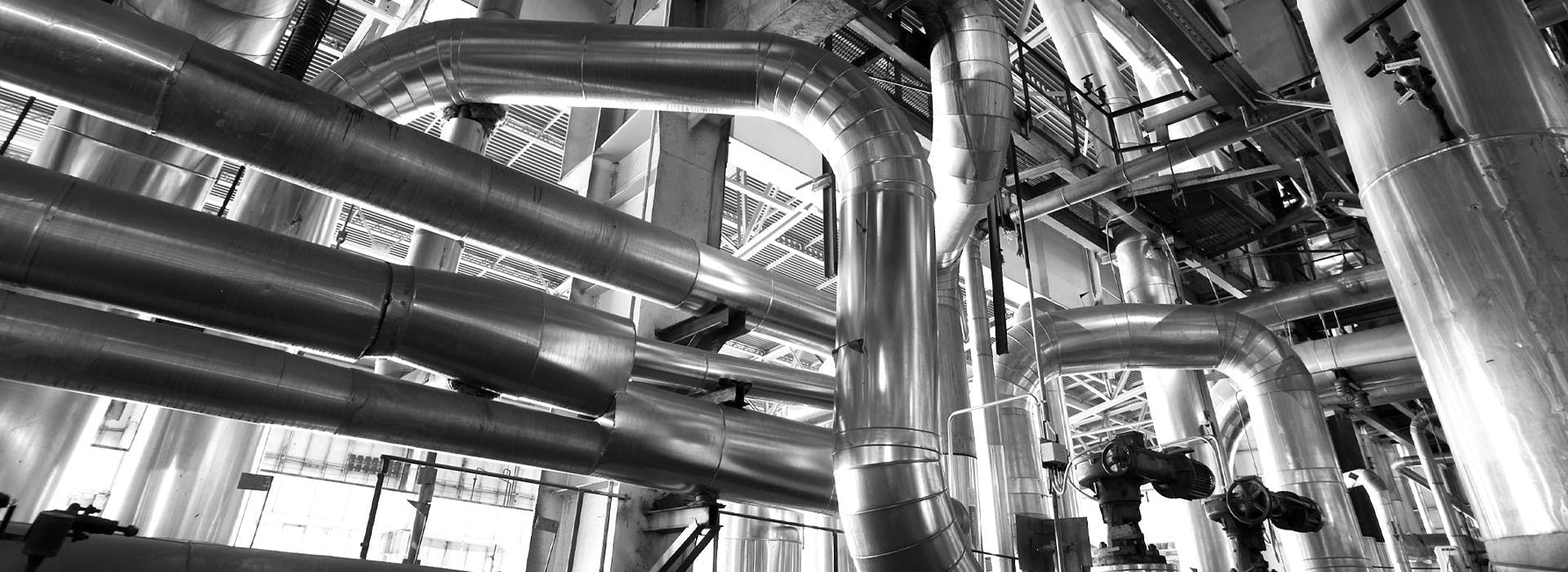
4. It’s all about strategy
Reducing downtime with obsolescence management
The majority of the developed world is heavily reliant on the oil, gas and coal industry. It accounts for a huge percentage of our global energy consumption and as a result, has become a thriving, but incredibly challenging industry.
As resources such as oil, gas and coal become increasingly limited, competition in the sector is increasing. To remain competitive companies can no longer rely on experience to choose where to drill. Instead they must innovate and invest in advanced technologies to improve accuracy.
Gathering real time data, for example, is crucial to both improve drilling accuracy and to schedule maintenance. Site managers can install sensors to monitor condition and anticipate any malfunctions.
Industry challenge
Companies in the oil and gas sector are investing in this new equipment to advance and remain competitive. Despite the increase in automation in the industry, some components currently used in these facilities have very short life spans.
Site managers may often find that parts are coming to the end of their lifespan and want to replace them. However, maintenance engineers often realise that the industrial equipment they use is no longer produced by the original equipment manufacturer (OEM). At this point, engineers must decide whether to purchase new equipment or source a spare from an obsolete parts provider.
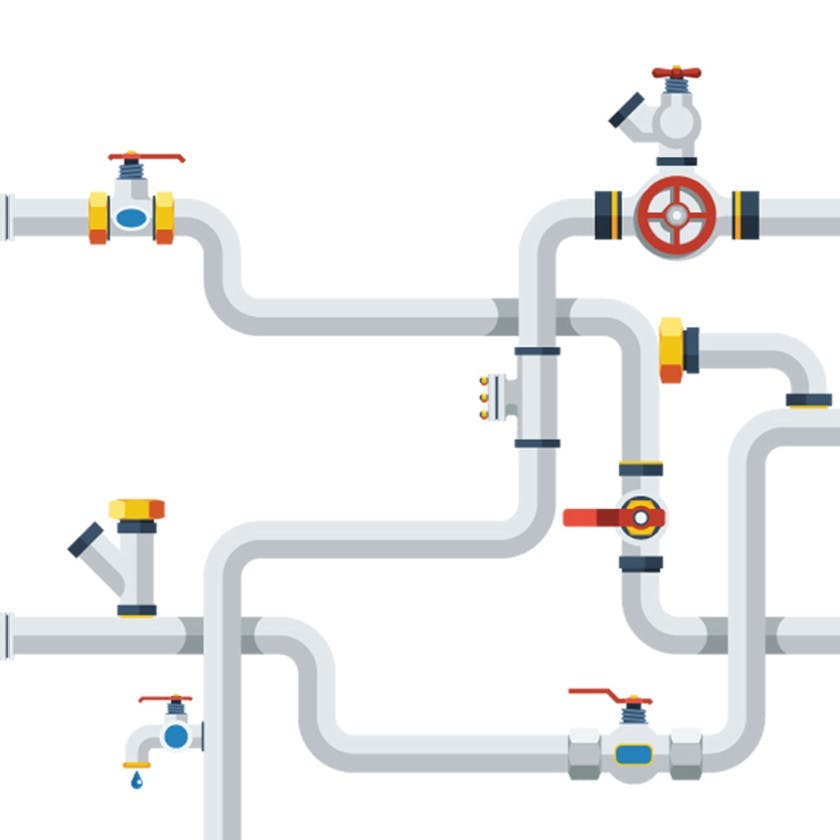
EU Automation’s solution
The best way to avoid the difficulties of obsolescence is to plan for the future. Engineers should be proactive and create a strategy that covers how to manage, mitigate and resolve obsolescence.
The first step is for organisations to identify the goals of the obsolescence plan, whether it is to save money, improve efficiency or simply to educate the workforce on obsolescence management. More often than not, a successful plan involves the combination of all three goals.
Oil and gas companies should focus on predicting which components may become obsolete and need replacing. The aim is to foresee all eventualities and plan for them.
By investing the time to assess a system and predict which components may become obsolete and need replacing, companies won't be struggling for a solution down the line when the problem occurs. This will reduce downtime, save money and uphold reputation.
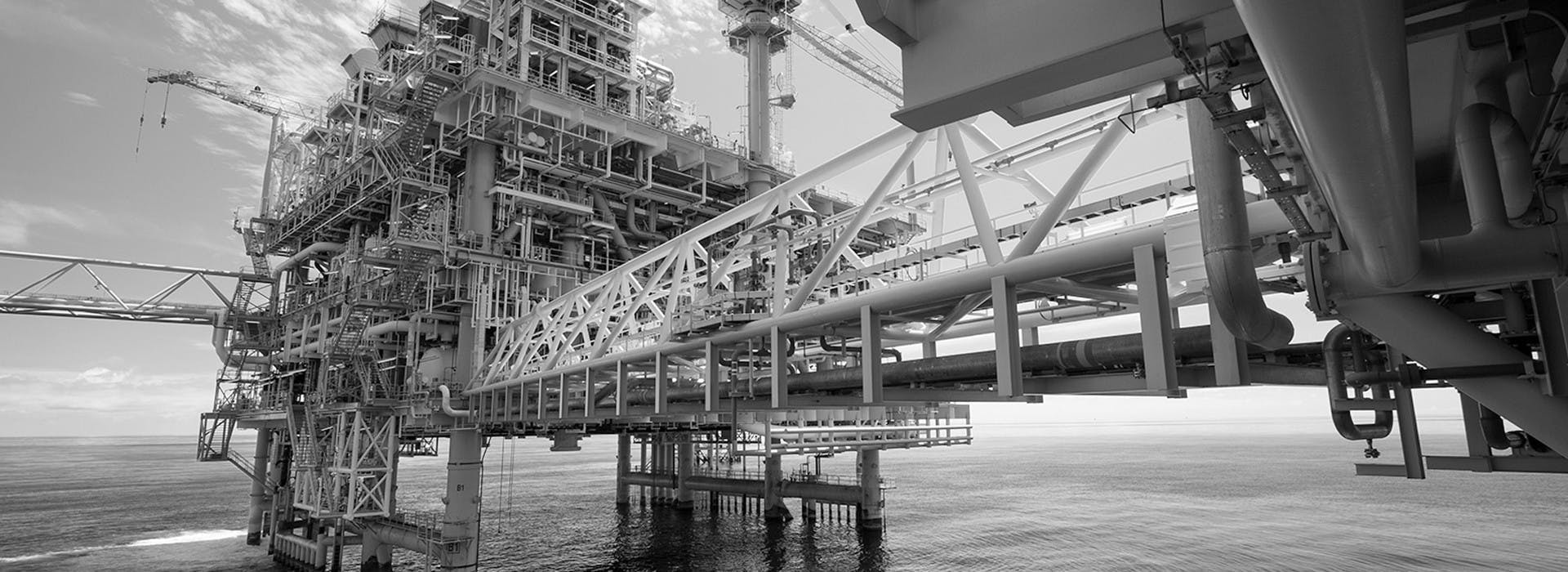
5. Keeping oil rigs afloat
According to Statista, there are currently over 1,300 offshore oil rigs operating across the world. Working in these inhospitable, remote environments can be difficult, particularly when considering maintenance. Any breakdown in remote locations will be costly — unexpected downtime currently costs the oil and gas industry an average of $42 million a year according to research by GE.
- A machine on the rig breaks down, stopping operations
- Downtime means that you will not be able to produce as much oil and may miss deadlines. This will be costly as staff in remote locations are left waiting and missing deliveries may negatively impact the business’ reputation
- You need to make quick decisions to return to production as soon as possible and get any new parts delivered to the rig
- Once you have found the faulty machine or part, you must decide how you will replace
- At this point you can buy an advanced, new machine that could be more efficient than your current equipment
- You should consider whether newer equipment will integrate into your current system
- Instead, you may want to repurchase the equipment you had before, but you find it is no longer sold by the original equipment manufacturer (OEM)
- At this point, you should contact EU Automation. We can source new, reconditioned and obsolete parts from global manufacturers
- We can deliver parts anywhere in the world in under 48 hours
- Once the part arrives, you can quickly install it and return to production
- You could consider implementing predictive maintenance, so that next time, you can replace a part before it causes unplanned downtime
- You can stay in contact with EU Automation to stock spares that you may need in the future, to avoid long periods of downtime
Explorar mais indústrias
Here to inspire you.
inspire
inspire
inspire
Receba atualizações regulares e informações sobre a automação real diretamente na sua caixa de correio.