Automating FSMA compliance with AI & robotics in food manufacturing
2024-08-07
6 min read
Leveraging automation for FSMA compliance
The Food Safety Modernization Act (FSMA) [1], enacted in 2011, represents a significant shift in the approach to food safety in the US. Instead of focusing solely on contamination response, FSMA [2] stresses the need of prevention. It gives the FDA new authority to regulate the way foods are grown, harvested, and processed.
It can be difficult for manufacturers to achieve these strict standards. The use of automation, however, can improve efficiency and safety while also assuring compliance.
The Food Traceability Final Rule, will be enforced starting January 20, 2026. This is under Section 204 of FSMA. This highlights the importance for manufacturers to embrace advanced technologies in order to maintain compliance.
Understanding FSMA compliance requirements
FSMA introduces comprehensive requirements [3] aimed at preventing food safety issues. These rules are meant to make sure that food manufacturers keep high standards throughout the whole process.
Preventive controls
Manufacturers are required to develop a written preventive control plan. This plan should identify potential hazards, preventive measures, and outline corrective actions to address any issues that may arise. This plan is a cornerstone of FSMA compliance, requiring continuous monitoring and updating to remain effective.
Record-keeping and documentation
Carefully kept records of safety procedures and compliance steps must be maintained. This documentation provides evidence of compliance and is crucial during FDA inspections. Automated systems can significantly simplify this process by ensuring accurate and up-to-date records are always available.
Supply chain oversight
Ensuring that all suppliers and ingredients comply with safety standards is essential. This can be made easier with the help of automated supply chain management systems.
Traceability and recall procedures
To keep track of products at all points in the supply chain, manufacturers need strong traceability tools. When it comes to safety issues, it is crucial to have efficient recall procedures in place. These steps are vital for minimising any potential risks to consumers. Automation can enhance traceability and streamline recall processes, making them more efficient and less error-prone.
The role of automation in FSMA compliance
Automation encompasses various technologies that can significantly enhance FSMA compliance. Automated systems reduce human error, ensuring consistent adherence to safety protocols. Take, for instance, the way automated filling and packaging lines can be calibrated to precise specifications. This calibration ensures that each product meets safety and quality standards without any variation.
Automated data collection and management systems streamline record-keeping, making it easier to track compliance and respond to audits. These systems have the ability to automatically log critical data points. This includes temperature controls and batch numbers. In this way, they make sure that all the important data is gathered correctly and quickly.
If you’re worried about the impact of human error, this is something automation can help to reduce. In this way, they make sure that all the important data is gathered correctly and quickly.
Machine learning and AI in the food industry for predictive food safety
Artificial Intelligence (AI) and machine learning are transforming food safety by enabling predictive analytics. A lot of data is analysed by these technologies in order to find trends and predict safety problems before they happen.
Anomaly detection in production processes
AI can keep an eye on production lines in real time and spot changes from the norm that could mean there are safety problems. For instance, if a temperature sensor detects an unusual spike, the system can alert operators to take corrective action immediately, preventing potential contamination.
Predictive maintenance of equipment
Machine learning algorithms can predict when equipment is likely to fail. This makes it possible to do repairs ahead of time and reduce downtime. By looking at old data and finding trends, these algorithms can plan maintenance before something breaks down. This makes sure that the system keeps running and meets safety standards.
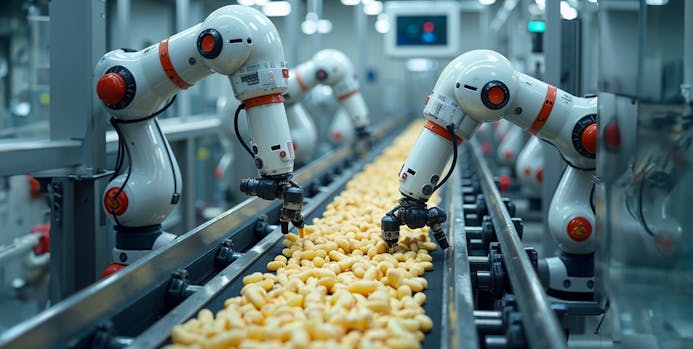
Monitoring and analysing supply chain data
AI has the incredible ability to analyse enormous amounts of data from various points in the supply chain. By doing so, it can detect patterns and trends that might suggest potential risks that are just starting to emerge. Companies that make things can be proactive and deal with possible problems before they get worse. This approach ensures the safety and integrity of the supply chain.
IBM’s Food Trust uses blockchain [4] and AI technology to enhance traceability and transparency. This enables companies to swiftly identify and address safety concerns. By leveraging these advanced technologies, manufacturers can enhance their predictive capabilities and maintain higher standards of food safety.
Robotics in food production for FSMA compliance
Robotics in food production plays a crucial role in maintaining high hygiene and safety standards. These advanced systems can perform a wide range of tasks that are essential for FSMA compliance.
Automated cleaning and sanitation
Robots can perform thorough and consistent cleaning, ensuring that facilities meet stringent hygiene standards. Automated cleaning systems can be programmed to clean at regular intervals. This helps reduce the risk of contamination and ensures a consistently high level of cleanliness.
Precision in food handling and packaging
Robotic systems can handle and package food with high precision, reducing the risk of contamination. Automated cleaning systems can be programmed to clean at regular intervals. This helps reduce the risk of contamination and ensures a consistently high level of cleanliness.
Continuous monitoring and real-time adjustments
Robots equipped with sensors can continuously monitor environmental conditions and make real-time adjustments to maintain optimal safety levels. For instance, if a robot detects a drop in temperature in a refrigerated area, it can automatically adjust the cooling system to restore the correct temperature.
Companies like Tyson Foods are investing in robotics to enhance food safety [5]. Tyson’s use of robotic systems for handling and packaging helps ensure consistent quality and compliance with safety standards.
Common obstacles of implementing automation for FSMA compliance
High initial costs
The upfront investment in automation technologies can be significant. Acquiring advanced systems such as AI-driven analytics, robotic process automation, and blockchain traceability solutions requires substantial financial outlay. This includes the cost of purchasing equipment, software, and infrastructure upgrades, as well as potential downtime during installation.
Technical complexity
Integrating new automation systems with existing processes and IT infrastructure can be technically complex. The complexity of this situation arises due to several factors. One of them is the need to ensure compatibility between old and new systems.
Another factor is the challenge of data migration. Also, there is the requirement for the seamless operation of automated processes without disrupting ongoing production.
Workforce adaptation
Introducing automation technologies often requires significant changes in workflows and job roles. Employees may need to adapt to new systems, learn new skills, and shift from manual tasks to overseeing automated processes. Resistance to change and a lack of necessary skills can be significant barriers.
Conclusion
The deadline for compliance with the Food Traceability Final Rule under Section 204 of FSMA is approaching on January 20, 2026. It is crucial to adopt advanced automation technologies as they are no longer optional, but essential. Manufacturers can enhance their overall food safety strategy by integrating AI, robotics, and blockchain. These technologies allow them to meet stringent requirements and ensure the highest level of safety.
At EU Automation, we provide a wide range of automation parts and solutions to help you achieve these goals. Explore our knowledge hub for more insights and stay ahead in the ever-evolving landscape of food safety.
Citations: